Introduction
When it comes to selecting materials for various applications, corrosion resistance is often a primary consideration. 410 stainless steel is a versatile alloy known for its unique combination of properties, including durability and resistance to corrosion. This article delves into the corrosion resistance of 410 stainless steel, exploring its characteristics, applications, and maintenance.
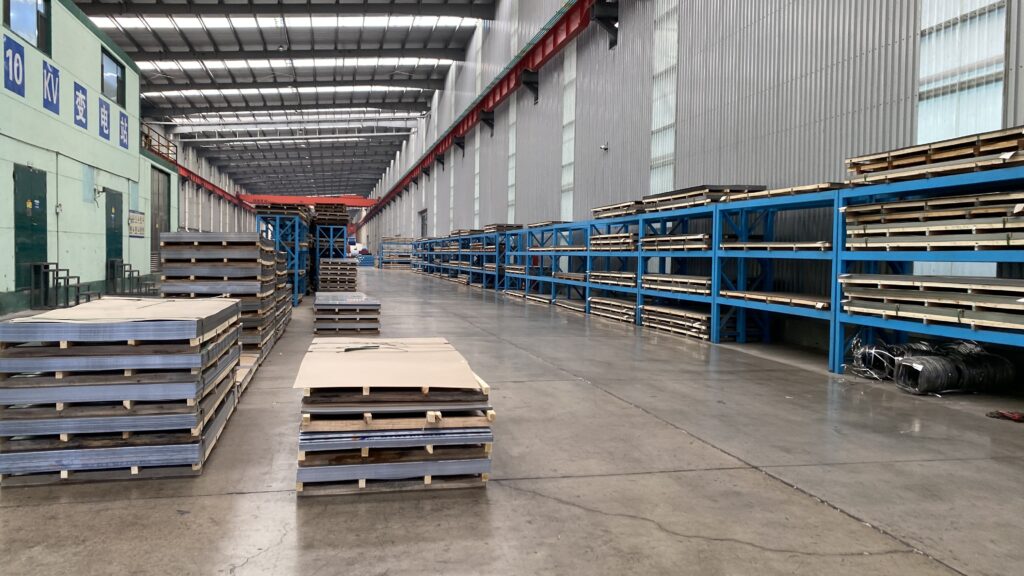
Understanding 410 Stainless Steel
What is 410 Stainless Steel?
410 stainless steel is a martensitic stainless steel that contains approximately 11.5% chromium, making it less corrosion-resistant than austenitic stainless steels. However, its unique composition provides sufficient toughness and strength for various applications. The alloy is commonly used in environments that require some level of corrosion resistance.
Composition of 410 Stainless Steel
The corrosion resistance of 410 stainless steel is largely influenced by its chemical composition. Below is a table summarizing its key components:
Element | Percentage (%) |
---|---|
Chromium | 11.5 – 13.5 |
Nickel | ≤ 1.0 |
Carbon | 0.15 – 0.25 |
Manganese | ≤ 1.0 |
Silicon | ≤ 1.0 |
Phosphorus | ≤ 0.04 |
Sulfur | ≤ 0.03 |
This composition allows 410 stainless steel to achieve a balance between hardness and corrosion resistance.
Corrosion Resistance Characteristics
How Does 410 Stainless Steel Resist Corrosion?
The primary factor that contributes to the corrosion resistance of 410 stainless steel is its chromium content. When exposed to oxygen, chromium forms a protective oxide layer on the surface, preventing further oxidation and rusting. This passive layer can be compromised in highly corrosive environments, but regular maintenance can help sustain its integrity.
Types of Corrosion Affecting 410 Stainless Steel
- Pitting Corrosion: Localized corrosion that leads to the formation of small pits on the surface.
- Crevice Corrosion: Occurs in stagnant solutions where the material is shielded from the bulk environment.
- Intergranular Corrosion: Occurs along the grain boundaries, particularly in welding areas.
Understanding these types of corrosion is vital for the effective use of 410 stainless steel in various applications.
Applications of 410 Stainless Steel
Industries Utilizing 410 Stainless Steel
410 stainless steel is commonly used in various industries due to its excellent strength and moderate corrosion resistance. Some typical applications include:
- Aerospace: Engine components and landing gear parts.
- Automotive: Exhaust valves and trim pieces.
- Construction: Structural supports and fasteners.
Benefits in Specific Applications
Application | Benefits of 410 Stainless Steel |
---|---|
Aerospace | High strength-to-weight ratio, good heat resistance |
Automotive | Cost-effective, corrosion-resistant exhaust components |
Construction | Durable fasteners that withstand environmental stress |
Maintenance Tips for 410 Stainless Steel
How to Maintain Corrosion Resistance
Proper maintenance can significantly enhance the longevity of 410 stainless steel products. Here are some essential maintenance tips:
- Regular Cleaning: Clean surfaces to remove contaminants that can lead to corrosion.
- Passivation: Apply passivation treatments to enhance the protective oxide layer.
- Protective Coatings: Use coatings to provide additional protection in harsh environments.
Signs of Corrosion
It’s essential to monitor for early signs of corrosion to address potential issues. Common indicators include discoloration, surface roughness, or visible pits.
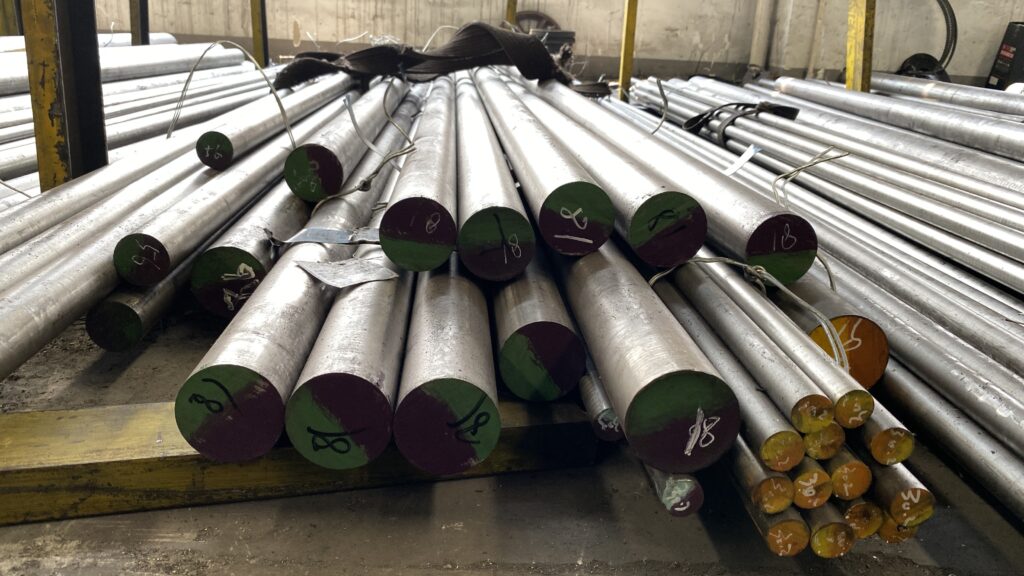
Conclusion
In summary, 410 stainless steel offers a unique combination of strength and moderate corrosion resistance, making it suitable for various applications. While it may not have the same level of corrosion resistance as austenitic stainless steels, proper maintenance and an understanding of its limitations can ensure its durability and effectiveness. By adhering to the maintenance tips outlined in this article, users can extend the life of their 410 stainless steel products.
FAQ
Q1: Is 410 stainless steel magnetic?
Yes, 410 stainless steel is magnetic due to its martensitic structure, which differentiates it from austenitic stainless steels.
Q2: Can 410 stainless steel be heat treated?
Yes, 410 stainless steel can be heat treated to improve hardness and strength, making it ideal for applications requiring enhanced mechanical properties.
Q3: How does 410 stainless steel compare to other stainless steels?
While 410 stainless steel offers good corrosion resistance, it is less resistant than austenitic stainless steels. However, it compensates with higher strength and hardness.
Q4: What industries primarily use 410 stainless steel?
410 stainless steel is used in aerospace, automotive, and construction industries, where strength and moderate corrosion resistance are required.
Q5: Can I weld 410 stainless steel?
Yes, 410 stainless steel can be welded, but proper techniques and precautions are necessary to minimize the risk of corrosion and maintain mechanical properties.
By understanding and implementing the information discussed in this article, users can effectively utilize 410 stainless steel in their applications while maximizing its corrosion resistance.