Introduction to 420 Stainless Steel
420 stainless steel is a versatile material known for its excellent corrosion resistance and moderate strength. However, achieving optimal performance requires careful consideration of its composition and usage.
Understanding 420 Stainless Steel Composition
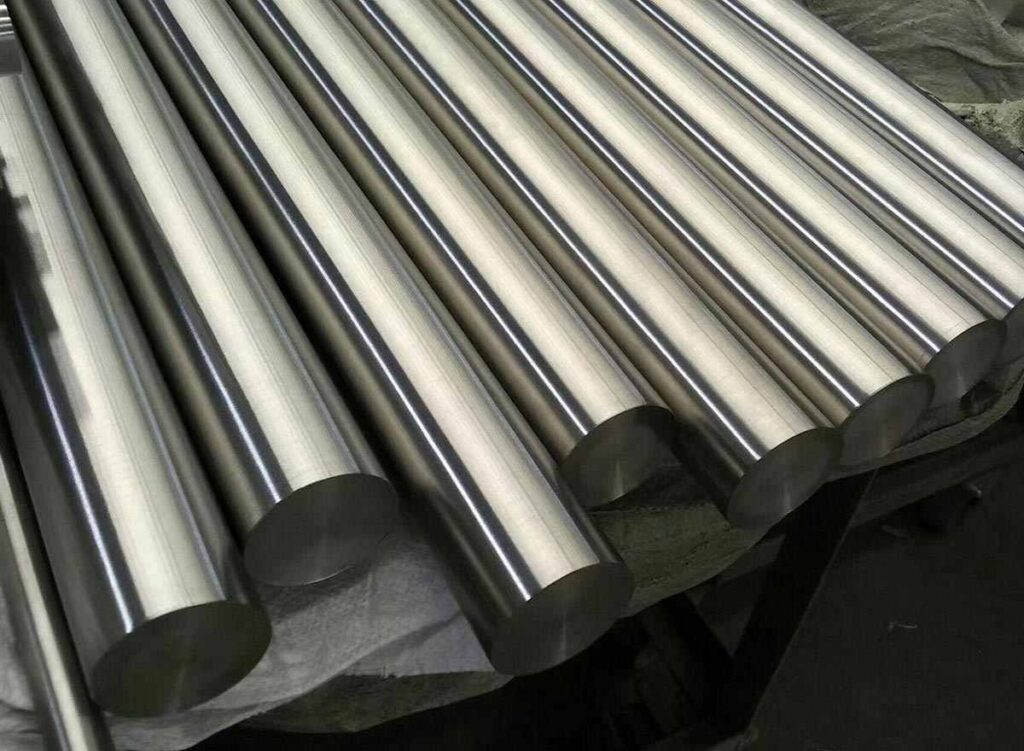
Chemical Composition
The chemical composition of 420 stainless steel is a defining factor in its properties and performance. Comprising approximately 0.15% carbon content, 420 stainless steel also contains around 12% chromium. This significant chromium presence contributes primarily to its corrosion resistance capabilities. Additionally, it incorporates a notable amount of manganese, about 1%, contributing to its hardness and strength.
Apart from these key elements, the composition may include small quantities of other elements such as silicon, phosphorus, sulfur, and sometimes nickel. These trace elements, although present in minor amounts, can influence specific characteristics of the steel, such as its machinability, weldability, and resistance to certain environmental factors.
Understanding the intricate balance and combination of these elements within the 420 stainless steel alloy is fundamental for comprehending its overall properties and suitability for diverse applications.
Properties of 420 Stainless Steel
420 stainless steel exhibits a unique set of properties that make it a sought-after material in various industries. Renowned for its moderate strength and excellent corrosion resistance, this alloy provides commendable hardness, making it suitable for applications requiring wear resistance and durability. Additionally, it boasts good machinability, enabling efficient shaping and fabrication processes.
Its ability to withstand mild corrosive environments is a notable attribute, although it may not be as resistant to corrosion as some higher-grade stainless steels. However, this alloy offers a fair balance between corrosion resistance and hardness, making it suitable for applications ranging from manufacturing components to cutlery and surgical instruments.
The combination of these properties renders 420 stainless steel versatile and valuable across multiple industries, where its specific characteristics cater to distinct operational requirements. Understanding these properties is pivotal for utilizing 420 stainless steel effectively in various applications.
Common Mistakes When Using 420 Stainless Steel
Common Mistakes When Using 420 Stainless Steel | Description |
---|---|
Avoiding Improper Heat Treatment | Proper heat treatment is pivotal for optimizing the properties and performance of 420 stainless steel. Incorrect procedures compromise hardness, strength, and functionality. Precise adherence to recommended heating, annealing, quenching, and tempering processes is crucial. Failure leads to hardness variations, reduced toughness, and structural flaws. |
Overlooking Corrosion Resistance | While 420 stainless steel possesses commendable corrosion resistance, neglecting this aspect leads to premature degradation. In intense or prolonged corrosive environments, limitations compared to higher-grade steels become apparent. Failure to consider specific corrosive conditions accelerates deterioration, affecting material integrity. Implementing protective measures like coatings and maintenance routines is vital. |
Ignoring Annealing Requirements | Annealing is critical for relieving internal stresses and enhancing mechanical properties. Ignoring specified annealing parameters impacts durability and performance. Non-adherence to recommended temperature, duration, and cooling rates retains stresses, compromising strength and fatigue resistance. Improper annealing affects microstructure, hardness, toughness, and machinability, impacting final product quality. |
Quality Issues and Pitfalls
Contamination Concerns
Contamination poses a significant risk to the quality and performance of 420 stainless steel during manufacturing, processing, or handling stages. Even minute levels of foreign substances can adversely affect the material’s properties and functionality.
Contamination can stem from various sources, including improper handling practices, inadequate cleaning of equipment, or mixing with other materials during fabrication. These contaminants, such as dirt, grease, or particles from other metals, can introduce flaws into the steel, compromising its structural integrity.
In severe cases, contamination can lead to localized corrosion, reduced mechanical properties, or even catastrophic failures in critical applications. Hence, stringent quality control measures and adherence to cleanliness protocols are essential to minimize the risk of contamination.
Surface Finishing Mistakes
Achieving the correct surface finish in 420 stainless steel is vital for both aesthetics and functionality. Mistakes in the surface finishing process can lead to compromised appearance, reduced corrosion resistance, and even structural issues.
Inadequate or improper surface finishing techniques, such as incorrect grinding, polishing, or buffing methods, can result in surface irregularities, scratches, or unevenness. These flaws not only affect the visual appeal but also create potential points for corrosion initiation and propagation.
Additionally, using inappropriate finishing tools or abrasive materials can leave residues or contaminants on the surface, hindering the material’s resistance to corrosion and potentially impacting its performance in different environments.
Best Practices for Working with 420 Stainless Steel
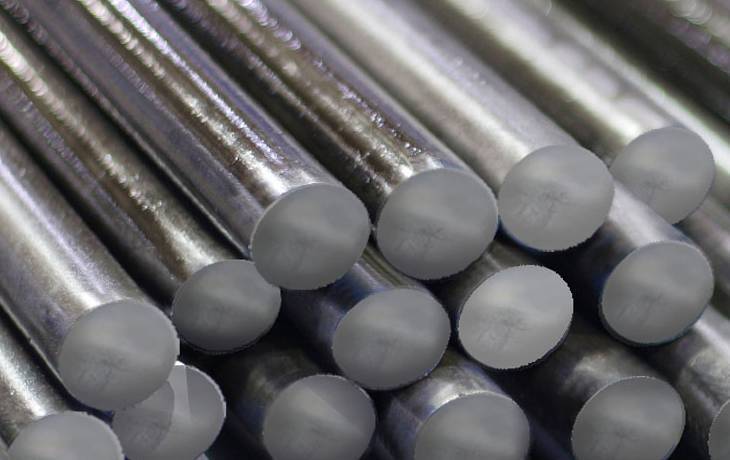
Proper Heat Treatment Techniques
Employing correct heat treatment methods is critical to unlocking the full potential of 420 stainless steel. Proper heat treatment enhances its mechanical properties, including hardness, strength, and corrosion resistance, ensuring optimal performance in various applications.
The process typically involves several stages, including annealing, quenching, and tempering. Annealing aims to relieve internal stresses and improve machinability by heating the steel to specific temperatures and allowing controlled cooling. Quenching involves rapidly cooling the heated steel to achieve the desired hardness, followed by tempering, which balances hardness and toughness by reheating and gradual cooling.
Accurate temperature control, precise heating and cooling rates, and proper holding times during each stage of heat treatment are crucial. Deviations from the recommended parameters can lead to inconsistencies in the material’s structure and properties.
Maintenance Tips
- Cleaning: Regularly clean 420 stainless steel surfaces using mild detergents and non-abrasive materials to remove dirt, debris, or contaminants. Avoid harsh cleaners or abrasive tools that could scratch the surface.
- Drying: After cleaning, ensure thorough drying of the stainless steel surfaces to prevent water spots or stains, which might affect its appearance and corrosion resistance.
- Protection from Corrosive Elements: Shield 420 stainless steel from prolonged exposure to corrosive substances or environments. Apply protective coatings or inhibitors to minimize the risk of corrosion, especially in harsh conditions.
- Avoiding Abrasive Contact: Prevent contact with abrasive materials or harsh chemicals that can damage the surface. Use soft cloths or brushes for cleaning to maintain the steel’s finish.
- Regular Inspection: Periodically inspect 420 stainless steel components for signs of corrosion, scratches, or damage. Early detection allows for timely intervention and prevents further deterioration.
Choosing the Right Applications
- Cutlery and Tools: 420 stainless steel’s moderate strength, corrosion resistance, and ease of fabrication make it suitable for manufacturing cutlery, knives, surgical instruments, and hand tools requiring good hardness and wear resistance.
- Industrial Components: It finds application in manufacturing components requiring moderate corrosion resistance and adequate strength, such as valves, pumps, shafts, and general-purpose machinery parts.
- Medical Instruments: Due to its ability to withstand sterilization processes and moderate corrosion resistance, 420 stainless steel is utilized in medical instruments and devices.
- Textile Industry: It’s used in textile industry components like needles or dyeing equipment due to its durability and resistance to staining.
- Cutting Blades and Shafts: The steel’s hardness and wear resistance make it suitable for manufacturing cutting blades, shafts, and molds where high mechanical strength and abrasion resistance are crucial.
Conclusion
In conclusion, 420 stainless steel offers a range of desirable properties, including moderate strength, corrosion resistance, and ease of fabrication, making it a valuable material across multiple industries. However, to harness its full potential, it’s essential to avoid common pitfalls and mistakes associated with its composition and usage.
Understanding the critical aspects such as proper heat treatment, corrosion resistance, annealing requirements, avoidance of contamination, and surface finishing mistakes is pivotal. Neglecting these aspects can compromise the material’s integrity, leading to reduced performance, premature degradation, or unexpected failures.
By adhering to proper heat treatment techniques, considering corrosion resistance, respecting annealing requirements, avoiding contamination, and ensuring precise surface finishing, users can optimize the functionality and durability of 420 stainless steel in diverse applications.
Applying the right maintenance practices and choosing suitable applications aligned with the steel’s properties further enhances its performance and extends its service life.
FAQs
Is 420 stainless steel suitable for outdoor applications?
420 stainless steel exhibits moderate corrosion resistance, making it suitable for some outdoor applications. However, prolonged exposure to harsh environments might require additional protection.
Can 420 stainless steel be welded?
Yes, 420 stainless steel can be welded, but it requires preheating and post-weld heat treatment to prevent cracking and maintain its properties.
What are the main benefits of using 420 stainless steel?
420 stainless steel offers good corrosion resistance, moderate strength, and ease of fabrication, making it suitable for various applications in industries like manufacturing, cutlery, and surgical instruments.
How does 420 stainless steel differ from other stainless steel grades?
Compared to some higher-grade stainless steels, 420 stainless steel has lower corrosion resistance but better hardness and wear resistance, making it more suitable for specific applications.
What are the limitations of 420 stainless steel?
While it offers good performance in many applications, 420 stainless steel might not be ideal for highly corrosive environments due to its moderate corrosion resistance.