Introduction
In the world of metallurgy, stainless steel has earned its place as a versatile and corrosion-resistant material. Among the myriad stainless steel grades available, two commonly used alloys, 410 and 316, stand out. Each alloy possesses distinct characteristics that make them suitable for various applications. In this article, we will delve into the differences between 410 stainless steel and 316 stainless steel, exploring their properties, uses, and how they compare in different scenarios.
Table of Contents
- Understanding Stainless Steel Alloys
- Composition and Properties
- 410 Stainless Steel
- 316 Stainless Steel
- Corrosion Resistance
- 410 Stainless Steel
- 316 Stainless Steel
- Strength and Durability
- Heat Resistance
- Magnetic Properties
- Applications
- 410 Stainless Steel
- 316 Stainless Steel
- Welding and Fabrication
- Cost Considerations
- 410 vs. 316: Which One to Choose?
- Real-World Examples
- Environmental Impact
- Maintenance and Care
- Innovations and Future Trends
- Conclusion
Understanding Stainless Steel Alloys
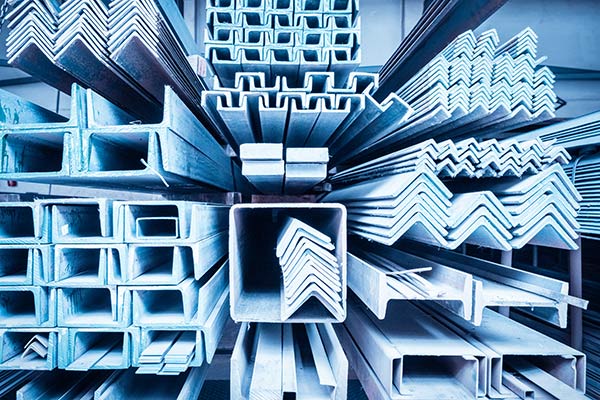
Stainless steel is an alloy primarily composed of iron, chromium, and other elements, with each grade exhibiting unique qualities. The 410 and 316 stainless steel alloys, while sharing some similarities, also have significant differences that make them suitable for distinct applications.
Composition and Properties
410 Stainless Steel
410 stainless steel is a martensitic alloy containing around 11.5% chromium. It is known for its high strength, moderate corrosion resistance, and hardness. The addition of carbon gives 410 steel its martensitic structure, making it capable of being heat treated for improved mechanical properties.
316 Stainless Steel
316 stainless steel, on the other hand, is an austenitic alloy with a higher chromium content of approximately 16-18%, along with nickel and molybdenum. This composition grants 316 steel superior corrosion resistance and excellent weldability, making it ideal for applications in harsh environments, such as marine settings.
Corrosion Resistance
410 Stainless Steel
While 410 stainless steel exhibits good corrosion resistance in dry atmospheres, it is less resistant to corrosion compared to 316 steel. It is susceptible to staining and pitting when exposed to chloride environments or acidic conditions.
316 Stainless Steel
316 stainless steel boasts remarkable corrosion resistance due to its higher chromium and molybdenum content. This alloy can withstand corrosion from chlorides, acids, and other corrosive agents, making it an exceptional choice for applications requiring exposure to harsh chemicals.
Strength and Durability
Both alloys are known for their strength, but 410 stainless steel is significantly harder and stronger than 316 steel due to its martensitic structure. This makes 410 steel suitable for applications where wear resistance and durability are crucial, such as in cutlery and industrial equipment.
Heat Resistance
316 stainless steel outperforms 410 steel in terms of heat resistance. Its austenitic structure allows it to maintain its mechanical properties even at high temperatures. This property makes 316 steel a preferred choice in applications involving elevated temperatures.
Magnetic Properties
410 stainless steel is magnetic due to its martensitic crystalline structure, while 316 stainless steel is non-magnetic due to its austenitic structure. The magnetic nature of 410 steel makes it suitable for applications where magnetism is required, such as magnetic shafts or sensors.
Applications
410 Stainless Steel
410 stainless steel finds its application in industries such as cutlery, surgical instruments, and valves due to its hardness and corrosion resistance in mildly corrosive environments.
316 Stainless Steel
316 stainless steel’s exceptional corrosion resistance makes it indispensable in industries like marine, pharmaceuticals, and food processing. It is used for making surgical implants, pipelines, and equipment exposed to saline environments.
Welding and Fabrication
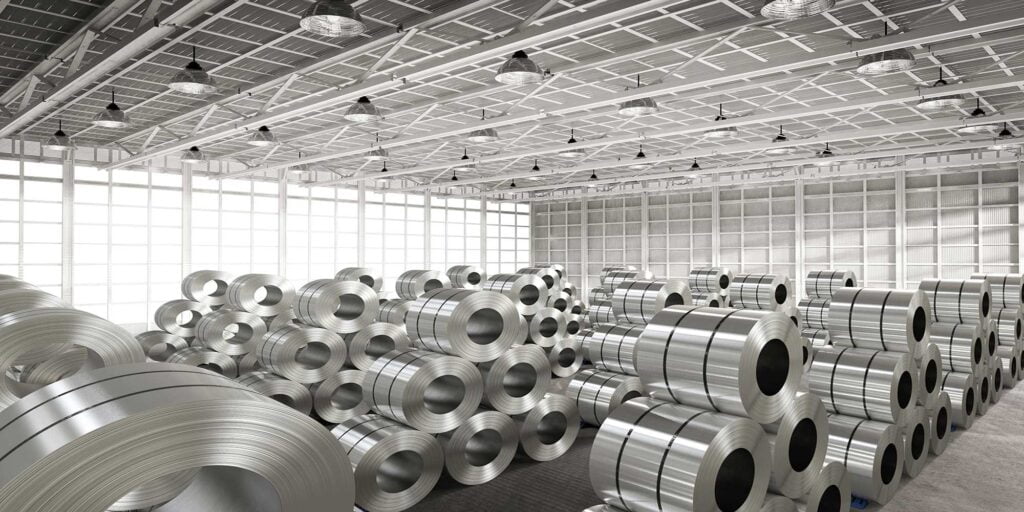
316 stainless steel is known for its superior weldability, whereas 410 steel requires preheating before welding and post-weld heat treatment to prevent cracking. This makes 316 steel more versatile and easier to work with during fabrication.
Cost Considerations
410 stainless steel is generally more cost-effective than 316 steel due to its simpler composition. However, the choice between the two alloys depends on the specific requirements of the application.
410 vs. 316: Which One to Choose?
The decision between 410 and 316 stainless steel depends on factors like corrosion resistance, strength, heat resistance, and application requirements. For harsh environments where corrosion resistance is paramount, 316 steel is the preferred choice. In applications demanding higher hardness and wear resistance, 410 steel may be more suitable.
Real-World Examples
In the marine industry, 316 stainless steel is extensively used for boat fittings, propellers, and underwater equipment due to its exceptional resistance to saltwater corrosion. On the other hand, 410 stainless steel’s hardness makes it a staple in the production of cutlery and kitchen utensils.
Environmental Impact
Both alloys are recyclable, contributing to their environmental sustainability. Proper recycling practices ensure that the raw materials used in stainless steel production are conserved.
Maintenance and Care
Regular cleaning and maintenance are essential for both 410 and 316 stainless steel to ensure their longevity and performance. Avoiding exposure to corrosive agents and adhering to recommended cleaning methods help preserve their appearance and properties.
Innovations and Future Trends
Advancements in metallurgical research continue to enhance the properties of stainless steel alloys, including 410 and 316. Researchers are exploring ways to improve corrosion resistance, strength, and other characteristics to meet evolving industry demands.
Conclusion
In the comparison between 410 stainless steel and 316 stainless steel, each alloy has its strengths and weaknesses that cater to specific applications. Whether it’s the hardness of 410 steel or the corrosion resistance of 316 steel, choosing the right alloy depends on the intended use and environmental conditions.
FAQs
- Is 410 stainless steel more durable than 316 steel?
While 410 steel is harder and more wear-resistant, 316 steel excels in corrosion resistance and heat resistance. - Can I weld 316 stainless steel without preheating?
Yes, 316 stainless steel is known for its excellent weldability, and preheating is often not required. - Which alloy is better for marine applications?
316 stainless steel is the preferred choice for marine applications due to its exceptional corrosion resistance in saltwater environments. - Can I use 410 stainless steel in acidic conditions?
410 stainless steel can be susceptible to staining and pitting in acidic conditions, so it’s not the ideal choice for such environments. - Are there other corrosion-resistant alloys worth considering?
Yes, apart from 410 and 316 stainless steel, alloys like 304, 2205, and 904L also offer unique properties suitable for specific applications.