Stainless steel is a popular material for a wide range of applications, and 316 stainless steel plates, in particular, have gained significant recognition due to their exceptional properties and versatility. In this article, we will explore the world of 316 stainless steel plates, from their composition to applications and everything in between. Let’s dive in!
Introduction to 316 Stainless Steel Plates
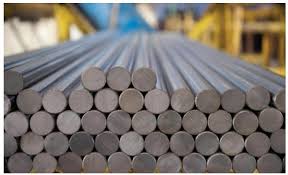
Stainless steel, a versatile and widely used material, encompasses numerous grades tailored to various industrial needs. Among these, 316 stainless steel plates shine as a prime example of excellence. This alloy, renowned for its remarkable properties and applications, stands out as a top choice for many professionals across different sectors.
316 stainless steel plates, often referred to simply as “316 plates,” boast exceptional corrosion resistance, coupled with remarkable strength and durability. They are celebrated for their ability to endure extreme temperatures and harsh environmental conditions. Beyond their functional benefits, these plates also exhibit an attractive aesthetic appeal, making them not only reliable but visually pleasing.
In this comprehensive exploration of 316 stainless steel plates, we will delve deep into their composition, properties, and the diverse applications that benefit from their unique attributes. By the end of this article, you will have a thorough understanding of why 316 stainless steel plates are considered a go-to solution in a multitude of industries, from food and beverages to pharmaceuticals and marine environments. So, let’s embark on this journey to unravel the secrets and advantages of 316 stainless steel plates.
The Composition of 316 Stainless Steel
The composition of 316 stainless steel, often referred to as “AISI 316” or “UNS S31600,” is a carefully balanced blend of various elements that endow it with its exceptional properties. This alloy primarily consists of iron, chromium, nickel, and molybdenum, with trace amounts of other elements contributing to its unique characteristics.
At its core, 316 stainless steel is primarily composed of iron, accounting for a substantial portion of its composition. This provides the base strength and structure necessary for its diverse applications.
Chromium, typically comprising around 16-18% of the alloy, plays a pivotal role in enhancing the corrosion resistance of 316 stainless steel. It forms a thin, passive oxide layer on the surface, which acts as a shield against corrosive agents, such as moisture and chemicals. This passive layer is what sets 316 stainless steel apart from its counterparts, making it highly resistant to rust and staining.
Nickel, another vital element, makes up approximately 10-14% of the alloy. It contributes to the overall durability of 316 stainless steel, aiding in its resistance to corrosion, especially in chloride-rich environments. The presence of nickel also grants this alloy its characteristic luster and finish, making it visually appealing for various applications where aesthetics are important.
Molybdenum, though present in relatively small amounts (approximately 2-3%), is a critical component of 316 stainless steel. It enhances the alloy’s resistance to pitting and crevice corrosion, making it exceptionally suitable for use in aggressive environments, such as marine and chemical settings.
Properties and Advantages of 316 Stainless Steel Plates
The properties and advantages of 316 stainless steel plates are a testament to the excellence of this alloy, making it a preferred choice across a diverse spectrum of industries. Let’s delve deeper into these remarkable attributes that set 316 stainless steel plates apart.
- Exceptional Corrosion Resistance: One of the standout properties of 316 stainless steel plates is their unparalleled resistance to corrosion. This resilience is primarily attributed to the presence of chromium and molybdenum in the alloy. Whether exposed to moisture, chemicals, or harsh environmental conditions, 316 stainless steel remains largely impervious to rust, staining, and deterioration.
- Strength and Durability: 316 stainless steel plates are renowned for their robustness. They possess excellent tensile strength and can withstand heavy loads and mechanical stress, making them ideal for structural applications. Moreover, their durability ensures a long service life, reducing the need for frequent replacements and maintenance.
- Temperature Resistance: Another distinctive property is the ability to endure extreme temperatures. 316 stainless steel plates retain their strength and integrity even when subjected to both high and low-temperature environments. This makes them suitable for applications ranging from cryogenic storage to high-temperature processing.
- Aesthetic Appeal: Beyond their functional advantages, 316 stainless steel plates offer an appealing aesthetic. The presence of nickel in the alloy imparts a lustrous and polished surface finish. This makes them an attractive choice for architectural and decorative applications, where appearance matters.
- Hygienic and Easy to Clean: In industries such as food and pharmaceuticals, hygiene is paramount. 316 stainless steel plates are not only resistant to corrosion but also easy to clean, making them the perfect choice for environments where cleanliness is of utmost importance.
- Biocompatibility: The biocompatibility of 316 stainless steel makes it an excellent choice for medical and pharmaceutical equipment. It can be safely used in contact with human tissues and fluids, which is crucial for implants and medical instruments.
- Non-reactive: This alloy is non-reactive with a wide range of substances, making it suitable for storing and transporting chemicals and other reactive materials without risk of contamination.
- Low Maintenance: The minimal maintenance requirements of 316 stainless steel plates translate to cost savings in the long run. Their resistance to corrosion and staining means they stay in optimal condition with little effort.
- Longevity: Due to their resistance to environmental factors, 316 stainless steel plates have an extended service life, reducing the need for frequent replacements and contributing to cost-effectiveness.
- Recyclability: 316 stainless steel is fully recyclable, making it an environmentally responsible choice.
Common Applications of 316 Stainless Steel Plates
The versatility of 316 stainless steel plates is highlighted by the wide array of applications they serve across various industries. These plates have earned their reputation as a reliable and high-performing material in demanding conditions. Let’s explore the common applications that benefit from the exceptional properties of 316 stainless steel plates.
- Marine Industry: 316 stainless steel’s resistance to corrosion, especially in saltwater environments, makes it an ideal choice for marine applications. It is used in boat fittings, shipbuilding, offshore oil rigs, and marine equipment, where exposure to corrosive elements is constant.
- Food and Beverage Processing: The hygienic properties of 316 stainless steel plates are crucial in the food and beverage industry. They are used in the production of equipment such as tanks, pipes, and conveyor systems to ensure food safety and easy cleaning.
- Pharmaceutical Sector: The pharmaceutical industry relies on 316 stainless steel for the production of sterile equipment and storage tanks. Its non-reactive and easy-to-clean nature ensures product purity and compliance with stringent regulations.
- Chemical Processing: In chemical plants, 316 stainless steel plates find use in reactors, vessels, and pipelines. Their resistance to a wide range of chemicals ensures the safe transport and storage of corrosive substances.
- Construction and Architecture: The aesthetic appeal of 316 stainless steel plates, coupled with their strength and durability, makes them a popular choice in architectural designs. They are used for facades, handrails, and structural elements in modern buildings.
- Medical and Healthcare: The biocompatibility of 316 stainless steel is crucial in the medical field. It is used for surgical instruments, implants, and medical devices where the material must not react with body tissues or fluids.
- Oil and Gas Industry: In the oil and gas sector, 316 stainless steel plates are employed in pipelines, valves, and equipment that must withstand aggressive environments, including exposure to chemicals and high pressures.
- Aerospace Engineering: The aerospace industry relies on the strength-to-weight ratio of 316 stainless steel for applications like aircraft components and structural elements, where both durability and reduced weight are essential.
- Automotive Manufacturing: In the automotive sector, 316 stainless steel is used in exhaust systems, catalytic converters, and other components that must withstand high temperatures and corrosive gases.
- Cryogenic Applications: The ability of 316 stainless steel to maintain its integrity at low temperatures makes it valuable in cryogenic applications, including storage tanks for liquefied gases like liquid nitrogen.
- Water Treatment: The resistance to corrosion and staining is advantageous in water treatment facilities, where 316 stainless steel is used in pumps, tanks, and pipelines for processing and distributing water.
- Energy Production: In power plants, 316 stainless steel plates find use in turbines, heat exchangers, and other components that must operate in high-temperature and high-pressure conditions.
- Environmental Engineering: The sustainability of 316 stainless steel is crucial in environmental engineering. It is used for equipment involved in waste management, recycling, and pollution control.
- Automated Machinery: Manufacturing and processing industries employ 316 stainless steel plates in automated machinery, ensuring smooth and reliable operations.
- Jewelry and Accessories: The aesthetic appeal of 316 stainless steel is embraced in the creation of jewelry and fashion accessories, where it offers an affordable and durable alternative to precious metals.
Comparing 316 Stainless Steel with Other Grades
When it comes to stainless steel, there are several grades available, each with its unique composition and properties. Comparing 316 stainless steel with other grades is essential to understand its specific advantages and where it excels. Let’s take a closer look at how 316 stainless steel stacks up against other common stainless steel grades.
- 316 vs. 304 Stainless Steel: One of the most common comparisons is between 316 and 304 stainless steel. While both offer excellent corrosion resistance, 316 stainless steel surpasses 304 in environments with high chloride concentrations. It is the superior choice for marine applications, thanks to its increased molybdenum content, which enhances its resistance to pitting and crevice corrosion.
- 316 vs. 316L Stainless Steel: 316L stainless steel is a low-carbon version of 316, with the “L” indicating reduced carbon content. This makes 316L more weldable and less susceptible to sensitization, a condition where the material becomes prone to corrosion. It is often preferred in applications involving extensive welding.
- 316 vs. 317 Stainless Steel: 316 and 317 stainless steel both contain molybdenum, which enhances their corrosion resistance. However, 317 stainless steel has a higher molybdenum content and additional alloying elements, making it even more resistant to corrosive substances. It is commonly used in chemical processing and pulp and paper industries.
- 316 vs. 321 Stainless Steel: While both grades are corrosion-resistant and suitable for high-temperature applications, 316 stainless steel is more versatile and has better overall performance. 321 stainless steel is preferred in applications that involve prolonged exposure to elevated temperatures, such as exhaust systems in aircraft and automotive.
- 316 vs. 430 Stainless Steel: Comparing 316 with 430 stainless steel highlights a significant difference in their corrosion resistance. 316 is highly resistant to corrosion, while 430 is less resistant, making it suitable for indoor applications like kitchen appliances but not for harsh environments.
- 316 vs. 2205 Duplex Stainless Steel: Duplex stainless steel like 2205 combines the best of both austenitic (316) and ferritic (430) stainless steels. It offers excellent corrosion resistance and high strength. The choice between 316 and 2205 depends on the specific application, with 2205 being suitable for more demanding conditions.
- 316 vs. 904L Stainless Steel: 904L stainless steel is extremely corrosion-resistant and is used in highly aggressive environments, such as the chemical and pharmaceutical industries. 316 is an excellent choice for most applications but may not match the superior corrosion resistance of 904L.
Manufacturing Process of 316 Stainless Steel Plates
The production of 316 stainless steel plates is a complex and meticulous process that involves several stages to ensure the highest quality and performance. Let’s explore the manufacturing process step by step.
- Melting and Refining: The process begins with the melting of raw materials in an electric arc furnace. The primary components, including iron, chromium, nickel, and molybdenum, are carefully weighed and added to the furnace. The intense heat of the furnace melts the materials, creating a molten alloy.
- Forming Ingots: Once the alloy is molten, it is cast into large rectangular molds, forming ingots. These ingots are allowed to cool and solidify. This initial shaping provides a foundation for subsequent processing.
- Hot Rolling: The ingots are then reheated and passed through a series of hot rolling mills. This process reduces the thickness of the material and shapes it into large, flat sheets or coils. Hot rolling also helps in homogenizing the material’s microstructure and improving its mechanical properties.
- Cold Rolling: After hot rolling, the material undergoes cold rolling. This process further reduces the thickness of the steel and refines its surface finish. Cold rolling imparts a smoother and more uniform surface to the plates, enhancing their aesthetic appeal.
- Annealing: To relieve internal stresses and improve the material’s corrosion resistance, the plates are annealed. They are heated to specific temperatures and then gradually cooled in a controlled environment. Annealing also allows for the adjustment of the material’s hardness and ductility.
- Cutting and Trimming: The plates are then cut to the desired dimensions using precision cutting machines. Trimming ensures that the edges are smooth and free of any irregularities.
- Finishing and Surface Treatment: The plates undergo various finishing processes, such as pickling and passivation, to remove any oxide layers and contaminants on the surface. This further enhances the corrosion resistance of the plates.
- Quality Control: At every stage of the manufacturing process, quality control measures are implemented. The plates are inspected for thickness, flatness, surface finish, and chemical composition to ensure they meet the specified standards.
- Packaging and Distribution: Once the plates pass quality control, they are packaged and prepared for distribution. Proper packaging is essential to protect the plates from damage during transportation.
Factors to Consider When Purchasing 316 Stainless Steel Plates
When purchasing 316 stainless steel plates, several crucial factors should be taken into account to ensure that you acquire the right product for your specific needs. These factors play a pivotal role in determining the quality, performance, and suitability of the plates for your application. Let’s delve into these considerations in greater detail:
- Plate Thickness: The thickness of 316 stainless steel plates is a fundamental factor. The required thickness will depend on the structural or functional demands of your application. Ensure that the selected thickness meets the mechanical requirements and design specifications.
- Plate Size and Dimensions: Consider the dimensions of the plates, including width and length, to ensure they fit seamlessly into your project or application. Custom sizing may be necessary to meet your exact requirements.
- Surface Finish: The surface finish of the plates is essential, especially in applications where aesthetics are a concern. Options include 2B, BA, and polished finishes. Choose a finish that aligns with your visual and functional needs.
- Corrosion Resistance: Assess the degree of corrosion resistance required for your application. 316 stainless steel is highly corrosion-resistant, but the specific environment and exposure to corrosive agents should influence your choice.
- Strength and Durability: Consider the mechanical properties of the plates, including their tensile strength and durability. Select a grade of 316 stainless steel that aligns with the load-bearing and durability requirements of your project.
- Certifications and Standards: Ensure that the plates meet industry standards and certifications. Look for materials that adhere to ASTM or other relevant standards to guarantee quality and reliability.
- Cutting and Fabrication Needs: If your project involves complex shapes or custom fabrication, consider the ease with which 316 stainless steel plates can be cut and shaped to meet your requirements. Consult with a fabricator if necessary.
- Weldability: Evaluate the weldability of the plates, especially if welding is part of your project. Some variations of 316 stainless steel, such as 316L, are preferred for their improved weldability.
- Budget and Cost: Cost is a significant consideration. While 316 stainless steel offers numerous advantages, it may come at a higher price point compared to other materials. Assess your budget and balance it with the benefits the material provides.
- Supplier Reputation: Choose a reputable supplier or manufacturer with a history of delivering quality stainless steel products. A reliable supplier ensures the plates meet your specifications and standards.
- Lead Times and Availability: Check the lead times and availability of the plates, as this can impact project timelines. Ensure that the plates can be delivered when needed.
- Environmental Impact: Consider the environmental impact of your choice. Stainless steel is recyclable, making it an environmentally responsible option. Evaluate the sustainability of your selection.
- Additional Services: Inquire about any additional services the supplier offers, such as cutting, surface treatment, or packaging, to simplify the procurement process.
Maintenance and Care Tips for 316 Stainless Steel
Maintaining the longevity and pristine appearance of 316 stainless steel is crucial for its optimal performance. Whether you’re using 316 stainless steel plates in a marine environment, food processing, or any other application, following proper maintenance and care tips is essential. Let’s explore these tips in detail:
- Regular Cleaning: To prevent the buildup of contaminants and maintain the aesthetic appeal, regularly clean the 316 stainless steel surfaces with mild soap or a stainless steel cleaner. Avoid abrasive cleaners or scouring pads that can scratch the surface.
- Direction of Cleaning: When cleaning, wipe the surface in the direction of the polish lines. This helps maintain the finish and minimizes the risk of scratching.
- Rinse Thoroughly: After cleaning, make sure to rinse the surfaces thoroughly with clean water. Residue from cleaning agents can leave streaks or stains on the stainless steel.
- Dry with a Soft Cloth: Use a soft, lint-free cloth to dry the surfaces. Avoid using abrasive or rough materials that can leave scratches.
- Avoid Harsh Chemicals: Refrain from using harsh chemicals, such as chlorine or hydrochloric acid, as they can damage the protective oxide layer on the stainless steel and result in corrosion.
- Passivation: In environments with higher risk of contamination or corrosion, consider passivating the stainless steel periodically. Passivation is a process that enhances the corrosion resistance of stainless steel by removing free iron and other impurities from the surface.
- Avoid Cross-Contamination: Prevent cross-contamination by segregating tools and equipment used with other materials that could transfer iron particles onto the stainless steel surfaces.
- Protection from Abrasive Particles: When used in industrial settings, shield the stainless steel surfaces from abrasive particles or materials that can scratch or damage the material.
- Inspect for Damage: Regularly inspect the stainless steel for any signs of damage, including scratches or dents. Promptly address any issues to prevent the initiation of corrosion.
- Repairs and Restoration: In case of visible damage or corrosion, consider professional repairs or restoration. Experienced technicians can remove stains, scratches, and restore the original finish.
- Proper Ventilation: In environments where 316 stainless steel is exposed to chemicals or fumes, ensure proper ventilation to minimize the risk of corrosion. Adequate ventilation prevents the buildup of corrosive substances on the surfaces.
- Lubrication: In applications involving moving parts, use appropriate lubrication to reduce friction and wear on the stainless steel components.
- Storage: If the stainless steel plates are not immediately used, store them in a clean, dry, and well-ventilated area. Avoid stacking them without proper protection, as this can lead to surface damage.
Environmental Impact and Sustainability
In an era where environmental consciousness is paramount, assessing the environmental impact and sustainability of materials like 316 stainless steel is crucial. This section delves into the eco-friendly aspects of 316 stainless steel and how it aligns with sustainable practices.
- Recyclability: One of the most notable environmentally friendly features of 316 stainless steel is its recyclability. It is a fully recyclable material, and the recycling process consumes significantly less energy compared to the production of primary steel. This not only reduces the demand for raw materials but also lessens the carbon footprint associated with steel production.
- Longevity and Durability: The longevity and durability of 316 stainless steel plates contribute to sustainability. Its resistance to corrosion means that the material can withstand harsh conditions and endure for decades, reducing the need for replacements and conserving resources in the long run.
- Low Maintenance: The minimal maintenance requirements of 316 stainless steel plates translate to cost savings and reduced environmental impact. Lower maintenance demands mean fewer chemicals and resources are required to keep the material in optimal condition.
- Biocompatibility: In medical and healthcare applications, the biocompatibility of 316 stainless steel ensures that it can safely interact with the human body, reducing the risk of adverse reactions and promoting the sustainability of medical equipment and implants.
- Resistance to Chemicals: In industries where 316 stainless steel is used to handle corrosive substances, the material’s resistance to chemicals reduces the need for secondary containment measures and safeguards, thus minimizing the potential for environmental contamination.
- Energy Efficiency: The energy efficiency of 316 stainless steel production, particularly in recycling processes, reduces the overall energy consumption in the steel industry, contributing to lower greenhouse gas emissions.
- Reduction of Waste: The minimal waste generated during the manufacturing process and the recyclability of stainless steel contribute to a reduction in overall waste production.
- Versatility and Adaptability: The versatility and adaptability of 316 stainless steel to various industries and applications allow for resource efficiency. One material can serve multiple purposes, reducing the need for different materials and their associated environmental impacts.
- Local Manufacturing: Locally sourcing 316 stainless steel plates can reduce transportation-related carbon emissions, as it reduces the distance the material needs to travel.
- Eco-Friendly Coating Options: The availability of eco-friendly surface treatment and coating options for stainless steel enhances its sustainability. These coatings can further enhance its resistance to environmental degradation.
- Regulatory Compliance: Manufacturers of stainless steel are increasingly adhering to strict environmental regulations and sustainability initiatives, further reducing the industry’s environmental footprint.
The Versatility of 316 Stainless Steel
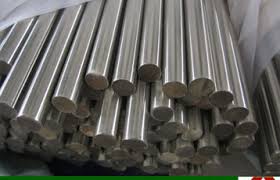
The versatility of 316 stainless steel is nothing short of remarkable, making it an indispensable material across a multitude of industries and applications. This section delves deeper into the various domains where 316 stainless steel’s adaptability shines, showcasing its capacity to meet diverse needs.
- Marine Applications: 316 stainless steel is the material of choice in marine environments, where it battles the corrosive effects of saltwater and constant exposure to the elements. From boat fittings to shipbuilding, it ensures the durability and safety of maritime structures and vessels.
- Food and Beverage Industry: The food and beverage sector benefits from 316 stainless steel’s hygienic properties. It is used for tanks, pipes, and equipment in the production and processing of food, ensuring the integrity and safety of consumables.
- Pharmaceuticals and Healthcare: In pharmaceutical and healthcare settings, 316 stainless steel is a trusted choice. Its biocompatibility and resistance to corrosion are critical for surgical instruments, medical implants, and equipment used in critical healthcare procedures.
- Chemical Processing: The chemical industry relies on 316 stainless steel for its robust resistance to various chemicals. It is employed in reactors, vessels, and pipelines for the safe transport and storage of corrosive substances.
- Construction and Architecture: The aesthetic appeal of 316 stainless steel is harnessed in architectural designs. It is used for facades, handrails, and structural elements in modern buildings, adding both strength and an attractive visual dimension.
- Oil and Gas Sector: In the oil and gas industry, 316 stainless steel stands up to the challenges of high-pressure and harsh chemical environments. It is used in pipelines, valves, and equipment that endure extreme conditions.
- Aerospace Engineering: The aerospace sector relies on 316 stainless steel for its strength-to-weight ratio. It is used in aircraft components and structural elements, ensuring both durability and reduced weight in aviation applications.
- Automotive Manufacturing: In the automotive sector, 316 stainless steel is the material of choice for exhaust systems and catalytic converters, where it can withstand high temperatures and the corrosive effects of exhaust gases.
- Cryogenic Applications: The ability of 316 stainless steel to maintain its integrity at low temperatures makes it a valuable choice in cryogenic applications, including storage tanks for liquefied gases such as liquid nitrogen.
- Water Treatment Facilities: In water treatment facilities, 316 stainless steel is used for pumps, tanks, and pipelines to ensure the processing and distribution of clean water.
- Energy Production: Power plants benefit from the high temperature and pressure resistance of 316 stainless steel. It is used in turbines, heat exchangers, and other components essential for energy production.
- Environmental Engineering: In waste management, recycling, and pollution control, 316 stainless steel plays a role in equipment that endures harsh conditions and contributes to sustainability.
- Automated Machinery: Manufacturing and processing industries employ 316 stainless steel in automated machinery to ensure efficient and reliable operations.
- Jewelry and Fashion Accessories: Its aesthetic appeal also finds a place in the creation of jewelry and fashion accessories, providing an affordable and durable alternative to traditional precious metals.
Pros and Cons of Using 316 Stainless Steel Plates
Understanding the advantages and disadvantages of using 316 stainless steel plates is vital in making informed decisions for various applications. This section explores the pros and cons in greater detail, helping you assess whether 316 stainless steel is the right choice for your specific needs.
Pros:
- Exceptional Corrosion Resistance: One of the primary advantages of 316 stainless steel plates is their extraordinary resistance to corrosion. They excel in environments where exposure to moisture, chemicals, and corrosive agents is a constant concern. This property extends their service life and minimizes maintenance needs.
- Strength and Durability: 316 stainless steel plates offer robust tensile strength and durability, making them ideal for applications that require structural integrity and the ability to withstand heavy loads or mechanical stress.
- Aesthetic Appeal: The presence of nickel in the alloy gives 316 stainless steel a lustrous and polished finish, making it an attractive choice for applications where aesthetics matter, such as architecture, design, and decorative elements.
- Temperature Resistance: These plates can endure a wide range of temperatures, from extreme cold to high heat, without compromising their structural integrity. This property is valuable in applications with varying temperature conditions.
- Hygienic and Easy to Clean: In industries like food processing and healthcare, the hygienic nature of 316 stainless steel is crucial. It’s easy to clean and maintain, ensuring the safety of consumables and the overall cleanliness of equipment.
- Biocompatibility: The biocompatibility of 316 stainless steel makes it an excellent choice for medical and pharmaceutical applications, where it comes into contact with human tissues and fluids.
- Non-Reactive: This alloy is non-reactive with a broad range of substances, making it suitable for storing and transporting chemicals, making it resistant to contamination.
- Low Maintenance: Minimal maintenance requirements translate to cost savings in the long run. 316 stainless steel plates retain their condition with little effort, reducing the need for frequent replacements.
- Recyclability: The plates are fully recyclable, aligning with sustainability goals and reducing the demand for new raw materials.
Cons:
- Cost: 316 stainless steel is often more expensive than other materials due to its unique properties and alloy composition. The initial investment cost can be higher, which might not be suitable for projects with strict budget constraints.
- Weight: In applications where weight is a critical factor, 316 stainless steel’s density can be a drawback. It is denser than other materials, which can impact transportation costs and structural considerations.
- Welding Challenges: While 316 stainless steel is weldable, it can be more challenging to work with compared to some other stainless steel grades. Careful handling and the use of appropriate techniques are necessary to ensure strong and durable welds.
- Availability: In some regions, there may be limited availability of 316 stainless steel plates, which can affect lead times and cost.
- Sensitization: In specific applications, 316 stainless steel can become susceptible to sensitization, which is a condition where the material becomes prone to corrosion in certain environments. This can be mitigated with the use of low-carbon variants like 316L.
Quality Standards and Certifications
When it comes to 316 stainless steel plates, adherence to quality standards and certifications is paramount. These benchmarks ensure that the material meets specific criteria and performs as expected. This section provides a deeper insight into the importance of quality standards and certifications in the context of 316 stainless steel plates.
- ASTM Standards: The American Society for Testing and Materials (ASTM) has established rigorous standards for stainless steel, including 316 stainless steel plates. These standards define the material’s composition, mechanical properties, and performance characteristics. Compliance with ASTM standards assures the material’s quality and consistency.
- ISO Certification: ISO (International Organization for Standardization) certification signifies that a manufacturing process or product complies with international quality management standards. ISO certification is often sought by manufacturers of 316 stainless steel plates to demonstrate their commitment to quality control and consistency.
- ASME Certification: The American Society of Mechanical Engineers (ASME) sets stringent standards for materials used in various industries, including 316 stainless steel plates. ASME certification is particularly important in applications involving high temperatures and pressures, such as in the oil and gas sector.
- NACE Compliance: The National Association of Corrosion Engineers (NACE) sets standards for materials and coatings used in corrosion control. NACE compliance is crucial in industries where 316 stainless steel plates are exposed to aggressive corrosive environments, such as chemical processing and marine applications.
- PED Certification: The Pressure Equipment Directive (PED) certification is essential for 316 stainless steel plates used in pressure vessels and equipment. It ensures that the material conforms to European Union standards for safety and performance.
- CE Marking: CE marking is required for stainless steel plates used in construction and architectural applications within the European Union. It indicates compliance with EU regulations and safety standards.
- Product Testing: Independent product testing, often carried out by certified laboratories, ensures that the material’s properties, such as corrosion resistance, mechanical strength, and chemical composition, meet specified standards.
- Material Traceability: Traceability of the material’s source and production process is critical. It provides assurance that the 316 stainless steel plates meet the required specifications and are not counterfeit or substandard.
- Third-Party Inspection: In some applications, third-party inspection by organizations like Lloyd’s Register or DNV (Det Norske Veritas) is essential to verify that the material complies with quality standards and project specifications.
- Regulatory Compliance: Various industries have specific regulations governing the use of materials, including 316 stainless steel plates. Ensuring regulatory compliance is vital to avoid legal issues and maintain the safety and integrity of the application.
- Client Requirements: Many clients have their own quality standards and specifications. Manufacturers must meet these requirements to supply stainless steel plates for particular projects or applications.
Market Trends and Availability
Understanding the current market trends and availability of 316 stainless steel plates is crucial for procurement and decision-making. This section delves into the market dynamics, emerging trends, and the availability of 316 stainless steel plates to provide a comprehensive overview.
Market Trends:
- Sustainability Emphasis: A notable trend in the stainless steel industry is the growing emphasis on sustainability. Both manufacturers and consumers are increasingly concerned about the environmental impact of materials. 316 stainless steel’s recyclability and long service life align with these sustainability goals.
- Demand in Renewable Energy: With the global push for renewable energy sources, there’s an increased demand for 316 stainless steel in the production of solar panels, wind turbines, and other renewable energy equipment. The material’s corrosion resistance and longevity make it ideal for these applications.
- Biomedical and Healthcare: The medical and healthcare sectors are witnessing growing demand for 316 stainless steel, particularly for surgical instruments and medical implants. The material’s biocompatibility and corrosion resistance are key drivers.
- Infrastructure Development: Infrastructure development in emerging economies is contributing to a surge in demand for 316 stainless steel plates. These plates are used in construction, transportation, and various civil engineering applications.
- Customization and Specialized Alloys: The industry is seeing a trend toward the production of specialized alloys to meet unique application requirements. This trend enables greater customization and adaptability to diverse industries.
- Digitalization and E-commerce: The digitalization of the stainless steel market has made it easier for buyers to source and purchase 316 stainless steel plates online. E-commerce platforms offer convenience, transparency, and a wider range of options.
Availability:
- Global Availability: 316 stainless steel plates are widely available across the globe, with production facilities in many countries. Major stainless steel manufacturers ensure a consistent supply to meet global demand.
- Local Suppliers: Local suppliers often stock 316 stainless steel plates and can provide quicker delivery for regional projects. Sourcing locally can also reduce transportation costs and environmental impact.
- Specialized Suppliers: Some suppliers specialize in high-quality 316 stainless steel products. They may offer additional services, such as cutting, surface treatment, and customization, to cater to specific needs.
- Lead Times: Availability and lead times can vary based on the region, supplier, and specific requirements. It’s essential to communicate with suppliers to ensure the timely delivery of 316 stainless steel plates for your project.
- Custom Orders: For specialized applications that require unique dimensions, finishes, or other specific attributes, custom orders may be necessary. Many suppliers can accommodate these requests, albeit with longer lead times.
- Stock and Inventory Management: Some industries, such as oil and gas, maintain strategic stock and inventory management practices to ensure a constant supply of 316 stainless steel plates for their ongoing operations.
Pricing and Cost Factors
Analyzing the pricing and cost factors associated with 316 stainless steel plates is a critical aspect of procurement and project budgeting. This section provides a detailed examination of the key factors that influence the pricing and overall costs of 316 stainless steel plates.
1. Raw Material Costs:The cost of the raw materials used to manufacture 316 stainless steel plates is a fundamental factor in determining their pricing. These materials include iron, chromium, nickel, molybdenum, and other alloying elements. Fluctuations in the prices of these base metals and alloying materials can significantly impact the overall cost of the plates.
2. Alloy Composition:The precise composition of the 316 stainless steel alloy can influence pricing. Variations such as the amount of nickel and molybdenum in the alloy can affect the material’s properties, including corrosion resistance and strength. Different grades within the 316 family, such as 316L (low carbon), may have different cost levels.
3. Market Demand:The demand for 316 stainless steel plates in the market plays a crucial role in determining their pricing. Higher demand can lead to increased prices, while lower demand can result in more competitive pricing. Market fluctuations, driven by global economic conditions and industry trends, can influence this factor.
4. Production Volume:The volume of production can impact pricing. Larger production runs often result in lower per-unit costs, as economies of scale come into play. Manufacturers that produce 316 stainless steel plates in larger quantities can offer more competitive prices to buyers.
5. Manufacturing Processes:The methods and processes used in manufacturing 316 stainless steel plates can influence costs. Technologically advanced and efficient manufacturing processes may lead to cost savings, which can be passed on to customers. However, more complex manufacturing methods, such as precision cutting or surface treatments, can add to the overall cost.
6. Transportation and Logistics:The cost of transporting 316 stainless steel plates to the end-user’s location is another significant factor. Factors such as distance, shipping method, and handling requirements can affect transportation costs. Local suppliers may offer cost advantages due to reduced transportation expenses.
7. Quality and Certification:Higher quality standards and certifications, such as ISO, ASME, or PED, may increase the cost of 316 stainless steel plates. These certifications ensure the material meets specific quality and safety standards, which can justify the premium in price.
8. Customization:Customization of 316 stainless steel plates to meet specific size, finish, or tolerance requirements can increase costs. Custom orders often involve additional processing and may require more extensive quality control measures.
9. Finish and Surface Treatment:The choice of finish and surface treatment for 316 stainless steel plates can influence pricing. Mirror finishes and specialized treatments, like pickling and passivation, can add to the cost due to the additional labor and materials involved.
10. Supplier and Location:The choice of supplier and their location can impact pricing. Different suppliers may offer varying price points for 316 stainless steel plates based on factors like reputation, service, and overhead costs.
11. Economic Conditions:Global economic conditions, such as inflation rates and currency exchange rates, can affect the pricing of 316 stainless steel plates. Fluctuations in exchange rates, for example, can impact the cost of imported materials and, subsequently, the final product’s price.
Conclusion
In conclusion, 316 stainless steel plates are a remarkable choice for a wide range of applications, offering exceptional corrosion resistance, strength, and versatility. Whether you’re in the construction, medical, or food industry, these plates are worth considering. Their sustainability and quality standards make them an excellent long-term investment.
FAQs
- Are 316 stainless steel plates suitable for outdoor applications?
Yes, they are highly resistant to corrosion, making them ideal for outdoor use. - How does 316 stainless steel compare to 304 stainless steel?
316 stainless steel offers superior corrosion resistance and is more suitable for marine environments. - Can 316 stainless steel plates be recycled?
Yes, stainless steel is 100% recyclable, making it an environmentally friendly choice. - What are the common surface finishes available for 316 stainless steel plates?
Common finishes include 2B, BA, and polished surfaces, each serving specific purposes. - Is 316 stainless steel plates more expensive than other stainless steel grades?
Yes, 316 stainless steel plates tend to be more expensive due to their higher nickel and molybdenum content, which enhances their properties.