In the world of construction and manufacturing, selecting the right materials is crucial. Among the plethora of materials available, 316 stainless steel square pipes stand out as a durable and versatile option. These pipes are widely used in various industries, thanks to their unique properties and advantages.
Properties and Advantages of 316 Stainless Steel
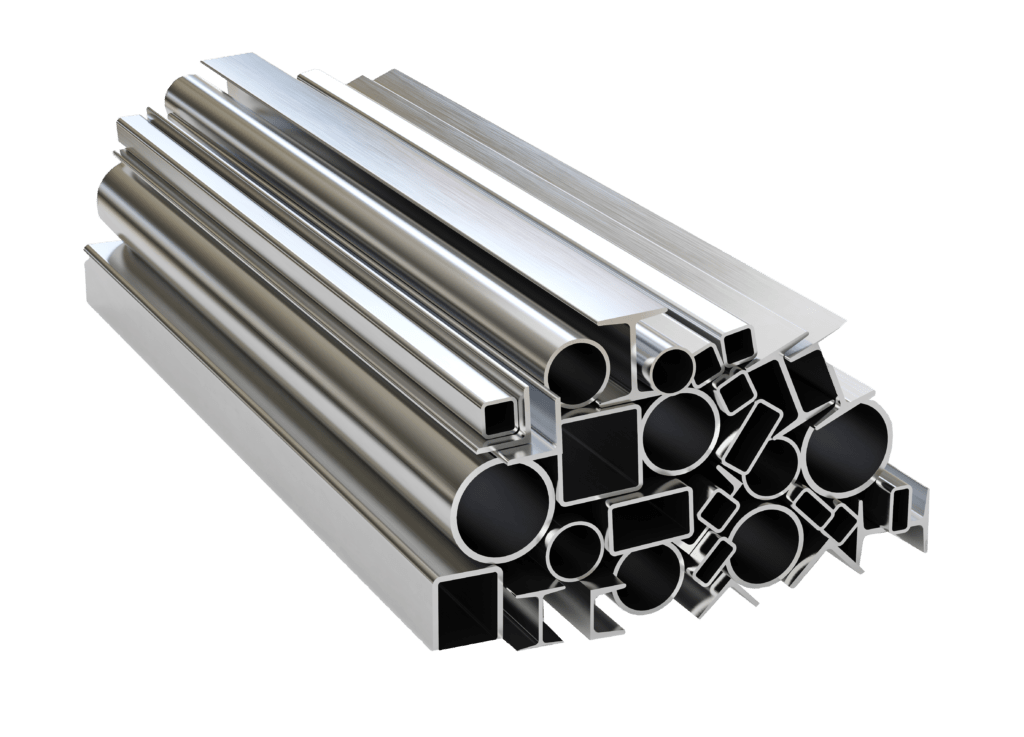
316 stainless steel is an austenitic stainless steel alloy that contains chromium, nickel, and molybdenum. These elements contribute to its remarkable properties, making it an ideal choice for square pipes:
High Corrosion Resistance
One of the most significant advantages of 316 stainless steel is its resistance to corrosion. It can withstand exposure to harsh environments, including marine and chemical settings, without losing its integrity.
Excellent Strength and Durability
316 stainless steel offers exceptional strength and durability, making it suitable for structural applications. It can handle heavy loads and is resistant to deformation.
Impressive Heat Resistance
This alloy retains its strength and structural integrity even at high temperatures, making it suitable for applications where temperature fluctuations are common.
Applications of 316 Stainless Steel Square Pipe
316 stainless steel square pipes find applications across various industries:
- Construction: These pipes are commonly used in the construction of buildings, bridges, and infrastructure due to their durability and structural integrity.
- Food and Beverage Industry: The non-reactive nature of 316 stainless steel makes it perfect for food processing equipment and storage.
- Chemical Industry: Its resistance to corrosion makes it a preferred choice for handling corrosive chemicals.
- Marine Applications: 316 stainless steel is highly suitable for marine environments due to its ability to resist saltwater corrosion.
Manufacturing Process of 316 Stainless Steel Square Pipe
The production of 316 stainless steel square pipes involves a series of intricate steps, transforming raw materials into the final product. Let’s take a closer look at this fascinating manufacturing process:
1. Melting and Formulation: The journey of a 316 stainless steel square pipe begins at the melting stage. High-quality raw materials, primarily iron ore, nickel, chromium, and molybdenum, are carefully selected and blended in precise proportions. This alloy formulation is critical because it directly influences the properties of the final product, including its corrosion resistance and strength.
2. Casting and Shaping: Once the alloy is perfected, it is melted in a furnace and then cast into various shapes. For square pipes, extrusion is a common method used. During extrusion, the molten metal is forced through a die to achieve the desired square shape. The precision of this process ensures uniform dimensions and consistent quality.
3. Heat Treatment: After shaping, the square pipe undergoes heat treatment. This involves subjecting the material to controlled temperatures and cooling rates to optimize its mechanical properties. Heat treatment enhances the pipe’s strength, durability, and resistance to high temperatures, ensuring it can withstand the demands of various applications.
4. Surface Finish: 316 stainless steel square pipes are typically given a polished or brushed finish. This not only enhances their visual appeal but also contributes to their resistance to corrosion. The smooth surface makes it more challenging for corrosive elements to adhere, further extending the product’s lifespan.
5. Inspection and Quality Control: Quality control is a fundamental part of the manufacturing process. Each square pipe is rigorously inspected to ensure it meets the required specifications and standards. This includes checking for dimensional accuracy, surface finish, and the absence of defects.
6. Cutting and Packaging: Once the square pipes pass inspection, they are cut to the desired lengths. This step ensures that the pipes are ready for distribution and use. They are then carefully packaged to protect them during transportation and storage.
Types and Sizes of 316 Stainless Steel Square Pipes
316 stainless steel square pipes come in a variety of types and sizes, catering to diverse industrial and construction needs. Let’s explore the different options available:
1. Types of 316 Stainless Steel Square Pipes:
- Welded Square Pipes: These are manufactured by welding together two edges of a flat strip of 316 stainless steel. Welded square pipes are known for their cost-effectiveness and are commonly used in structural applications.
- Seamless Square Pipes: Seamless pipes are created without any welding seams, making them highly resistant to leaks and corrosion. They are preferred in applications where fluid flow or gas transport is crucial.
2. Sizes of 316 Stainless Steel Square Pipes:
- 1″ x 1″ Square Pipe: This size is often used in handrails, architectural structures, and decorative applications.
- 2″ x 2″ Square Pipe: A larger size, suitable for applications requiring higher strength, such as frames for heavy machinery or support structures.
- 3″ x 3″ Square Pipe: These square pipes are used in more robust applications like building columns and support beams.
- Custom Sizes: Manufacturers can produce 316 stainless steel square pipes in custom sizes to meet specific project requirements. This flexibility ensures that the material can be tailored to diverse applications.
3. Wall Thickness:
- The thickness of the walls can vary depending on the application. Common thicknesses range from 1.5mm to 6mm, with thicker walls providing increased strength and durability.
The choice of type and size of 316 stainless steel square pipe depends on the specific requirements of the project. Factors such as load-bearing capacity, corrosion resistance, and cost considerations play a significant role in determining the most suitable option. The availability of custom sizes allows for tailored solutions that can meet even the most unique and demanding applications in industries such as construction, manufacturing, and infrastructure.
Corrosion Resistance of 316 Stainless Steel
The exceptional corrosion resistance of 316 stainless steel is a key attribute that sets it apart from other materials. Let’s take a closer look at the factors that contribute to its impressive ability to withstand the corrosive forces of various environments:
1. Passive Layer Formation: 316 stainless steel contains chromium and molybdenum, which are essential for the formation of a passive layer on the surface of the material. This passive layer acts as a shield, creating a protective barrier between the metal and the corrosive elements in the environment. Even in harsh conditions, such as exposure to saltwater, chemicals, or acidic solutions, this passive layer remains intact, effectively preventing corrosion.
2. Pitting Resistance: One of the notable features of 316 stainless steel is its resistance to pitting corrosion. Pitting occurs when small pits or craters form on the surface of the material due to localized corrosion. The alloy’s composition and the passive layer’s stability make it highly resistant to these types of corrosive attacks, ensuring the material retains its integrity over time.
3. Chloride Resistance: 316 stainless steel is particularly renowned for its ability to resist chloride-induced corrosion. This makes it an excellent choice for applications in marine environments, where exposure to saltwater and brine is frequent. It can withstand the corrosive effects of chlorides, which can rapidly degrade other metals.
4. Acid Resistance: In chemical and industrial settings, where acids are present, 316 stainless steel remains unscathed. It can resist the corrosive effects of both organic and inorganic acids, including sulfuric acid and hydrochloric acid. This acid resistance makes it suitable for various chemical processing equipment.
5. High-Temperature Corrosion Resistance: Many metals and alloys become susceptible to corrosion at elevated temperatures. However, 316 stainless steel maintains its corrosion resistance even in high-temperature environments, making it suitable for applications where heat is a factor.
Welding and Fabrication of 316 Stainless Steel Square Pipe
Welding and fabricating 316 stainless steel square pipes require precision and expertise to ensure that the material retains its exceptional properties, particularly its corrosion resistance. Let’s delve deeper into the intricate process of working with this versatile alloy:
1. Welding Techniques: Welding 316 stainless steel square pipes demands the use of specific techniques to maintain the material’s corrosion-resistant properties. TIG (Tungsten Inert Gas) and MIG (Metal Inert Gas) welding are commonly employed methods. These techniques provide precise control over the heat input and shielding gas, minimizing the risk of heat-affected zone (HAZ) corrosion.
2. Selection of Filler Materials: Choosing the right filler material is crucial in welding 316 stainless steel. Matching the filler material to the base metal, in terms of composition and corrosion resistance, is essential. Commonly used fillers include 316L or 308L, which help maintain the alloy’s resistance to corrosion in the welded areas.
3. Post-Weld Cleaning: After welding, thorough cleaning is necessary to remove any contaminants, such as oxides or carbides, that may have formed during the welding process. Proper cleaning ensures the restoration of the passive layer, which is vital for corrosion resistance. Acid pickling or passivation can be employed to achieve this.
4. Fabrication Techniques: Fabrication of 316 stainless steel square pipes encompasses various processes, including cutting, bending, and shaping. High-quality tools and machinery are essential to ensure precise and clean cuts without causing structural damage.
5. Precision Measurements: Accurate measurements and precision in fabrication are critical to achieve the desired dimensions and maintain the integrity of the material. Proper alignment and welding techniques are essential to prevent distortion or stress on the square pipe.
6. Corrosion Prevention: After welding and fabrication, it’s essential to consider corrosion prevention methods, particularly if the square pipes will be used in corrosive environments. This may involve applying additional protective coatings or treatments to maintain the material’s resistance to corrosion at the weld joints.
7. Quality Control: Stringent quality control measures are imperative in the welding and fabrication of 316 stainless steel square pipes. This includes non-destructive testing (NDT) methods like ultrasonic testing or radiographic inspection to ensure the integrity of the welded joints.
Maintenance and Care
Ensuring the longevity and optimal performance of 316 stainless steel square pipes requires proper maintenance and care. Here’s a detailed look at how to maintain these pipes effectively:
1. Regular Cleaning: Regular cleaning is the foundation of stainless steel maintenance. To remove dirt, dust, and contaminants, use a mild detergent or a stainless steel cleaner. Apply it with a soft cloth or sponge, following the grain of the steel for the best results. Rinse thoroughly and dry to prevent water spots or streaks.
2. Preventing Surface Damage: Avoid using abrasive materials, scrubbers, or steel wool for cleaning, as they can scratch the surface and compromise its corrosion resistance. Additionally, steer clear of cleaners with high chloride content, as they can lead to surface pitting.
3. Passivation: Passivation is a chemical process that helps restore the passive layer on the stainless steel surface. If the passive layer is damaged due to welding or fabrication, passivation can be employed to rebuild it. This process helps maintain the steel’s corrosion resistance.
4. Inspection: Regular inspections are crucial to identify any signs of damage, corrosion, or discoloration. Early detection allows for timely intervention and prevents minor issues from escalating into more significant problems.
5. Removing Rust Stains: While 316 stainless steel is highly resistant to corrosion, it is not entirely immune. Rust stains can occur when contaminants such as carbon steel or iron come into contact with the surface. To remove rust stains, use a rust remover or a mixture of baking soda and water. Always rinse and dry thoroughly after cleaning.
6. Lubrication: For components that move or pivot, such as hinges or joints, periodic lubrication with a stainless steel-compatible lubricant can prevent wear and ensure smooth operation.
7. Protecting Against Chlorides: In coastal or marine environments, where exposure to chlorides is common, it’s essential to rinse the stainless steel surface with fresh water regularly. This helps remove salt deposits that could lead to corrosion over time.
8. Environmental Considerations: Environmental factors can also influence maintenance. In polluted or industrial areas, more frequent cleaning may be necessary to remove airborne contaminants that can settle on the steel’s surface.
9. Documentation: Maintain detailed records of maintenance activities, including cleaning schedules, passivation dates, and any repairs or alterations. This documentation helps in tracking the steel’s condition over time and planning for necessary maintenance.
Comparing 316 Stainless Steel with Other Alloys
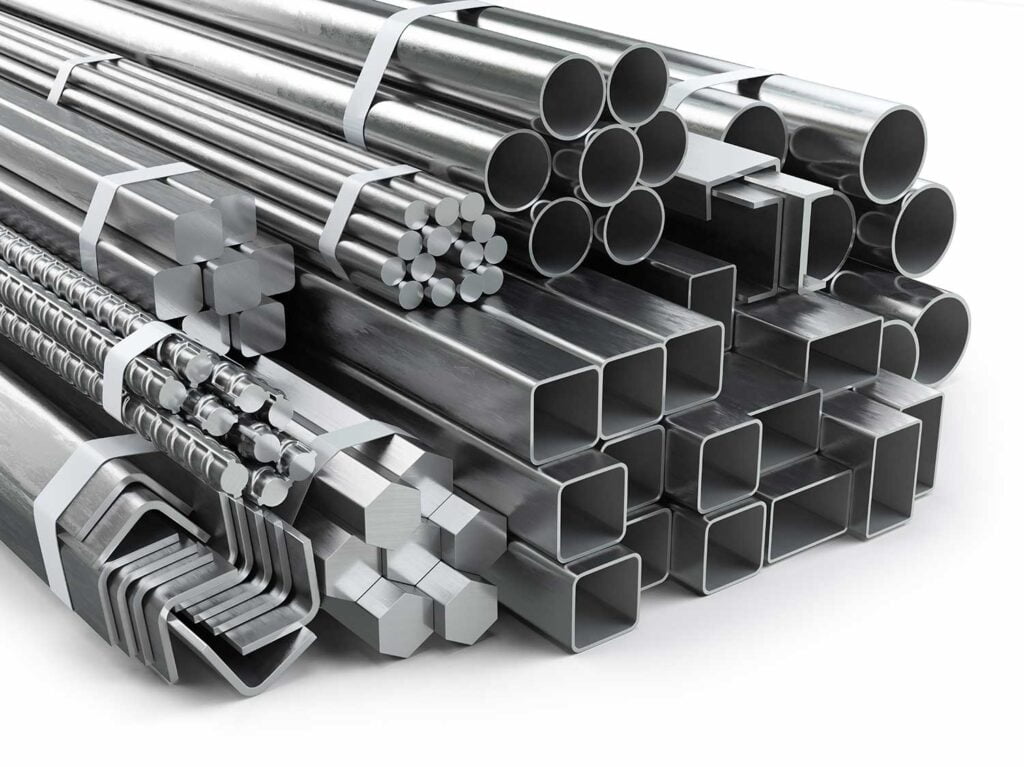
When selecting materials for various applications, it’s essential to consider the advantages and disadvantages of different alloys. Comparing 316 stainless steel with other alloys reveals the unique qualities that set it apart:
1. 316 Stainless Steel vs. 304 Stainless Steel:
- Both 304 and 316 stainless steel are popular choices, but 316 offers superior corrosion resistance due to its higher molybdenum content. This makes it the preferred option for applications exposed to corrosive environments, such as marine or chemical settings.
2. 316 Stainless Steel vs. Carbon Steel:
- Unlike carbon steel, 316 stainless steel is corrosion-resistant. It can withstand exposure to moisture, chemicals, and saltwater without rusting or deteriorating, making it suitable for outdoor and marine applications. Carbon steel, on the other hand, is susceptible to corrosion without protective coatings.
3. 316 Stainless Steel vs. 316L Stainless Steel:
- 316L is a low-carbon version of 316 stainless steel, designed to further enhance its corrosion resistance. While both alloys offer excellent resistance to corrosion, 316L is even more resistant to sensitization, making it ideal for applications involving welding.
4. 316 Stainless Steel vs. 316Ti Stainless Steel:
- 316Ti stainless steel contains titanium, which provides increased resistance to sensitization during welding. This makes 316Ti a suitable choice for applications where elevated temperatures and welding are involved.
5. 316 Stainless Steel vs. 317 Stainless Steel:
- 317 stainless steel contains higher levels of molybdenum and nickel compared to 316. This gives it superior resistance to chloride-induced pitting and crevice corrosion, making it a better option for extremely corrosive environments.
6. 316 Stainless Steel vs. Aluminum:
- While aluminum is lightweight and offers good corrosion resistance, it cannot match the strength and durability of 316 stainless steel. In applications requiring structural integrity and resistance to extreme conditions, 316 stainless steel is the superior choice.
7. 316 Stainless Steel vs. Duplex Stainless Steel:
- Duplex stainless steel combines the qualities of austenitic and ferritic stainless steels, offering high strength and excellent corrosion resistance. However, it is often more expensive than 316 stainless steel and may be over-engineered for certain applications.
Cost Considerations
When deciding on materials for a project, cost considerations play a pivotal role. 316 stainless steel, while offering a wide array of advantages, may involve higher upfront costs compared to some other materials. Here’s a closer look at the cost factors to keep in mind:
1. Initial Material Cost:
- One of the primary cost considerations is the initial price of 316 stainless steel. It is typically more expensive than materials like carbon steel or aluminum. This can be a significant factor in budget-conscious projects, especially when large quantities of material are required.
2. Durability and Longevity:
- While 316 stainless steel may have a higher initial cost, it offers remarkable durability and a longer lifespan. Its resistance to corrosion, even in harsh environments, can result in significant cost savings over time. Reduced maintenance and replacement costs can outweigh the initial investment.
3. Maintenance Costs:
- The minimal maintenance requirements of 316 stainless steel can lead to substantial long-term savings. Other materials may demand regular maintenance, protective coatings, or replacements due to corrosion, all of which incur additional costs.
4. Reduced Downtime:
- Projects that utilize 316 stainless steel may experience reduced downtime, as the material’s corrosion resistance minimizes the need for repairs and replacements. This can lead to improved efficiency and less operational disruption, ultimately translating into cost savings.
5. Environmental Impact:
- The environmental benefits of 316 stainless steel can also have financial implications. Its 100% recyclability reduces waste and can potentially lead to cost savings related to waste disposal and environmental compliance.
6. Total Cost of Ownership:
- To make an informed decision, it’s important to consider the total cost of ownership. This encompasses not only the initial material cost but also maintenance, replacement, and operational costs over the lifetime of the project. In many cases, the total cost of ownership for 316 stainless steel can be more favorable than materials that seem cheaper upfront.
Environmental Sustainability
Environmental sustainability is a critical aspect of material selection, and 316 stainless steel has several qualities that contribute to its eco-friendliness:
1. Recyclability:
- One of the most significant environmental advantages of 316 stainless steel is its recyclability. It is 100% recyclable, meaning it can be reused and repurposed indefinitely. Recycling stainless steel reduces the demand for raw materials, conserving natural resources and reducing the environmental impact of mining and ore extraction.
2. Longevity:
- 316 stainless steel is renowned for its long lifespan. Its resistance to corrosion, even in harsh conditions, ensures that products made from this material have an extended operational life. This longevity results in fewer replacements and less waste, further contributing to sustainability.
3. Reduced Maintenance:
- The minimal maintenance required for 316 stainless steel products reduces the use of cleaning chemicals and the generation of hazardous waste. This is particularly beneficial in industries where other materials might necessitate more frequent maintenance and cleaning.
4. Energy Efficiency:
- The production of 316 stainless steel has become increasingly energy-efficient over the years. Modern manufacturing processes consume less energy, resulting in a reduced carbon footprint compared to older production methods.
5. Lower Environmental Impact:
- 316 stainless steel’s corrosion resistance and longevity help reduce the environmental impact of construction and industrial projects. It lowers the need for frequent replacements or repairs, which can be resource-intensive and environmentally detrimental.
6. End-of-Life Recycling:
- Even when 316 stainless steel products reach the end of their useful life, they can be easily recycled. This contributes to a circular economy, where materials are continually reused, reducing the volume of waste sent to landfills.
7. Sustainable Certifications:
- Some manufacturers produce 316 stainless steel with a focus on sustainable practices. They may obtain certifications and adhere to standards that promote environmental responsibility throughout the production process.
Conclusion
In conclusion, 316 stainless steel square pipes are a superb choice for various applications due to their exceptional properties and durability. Their corrosion resistance, heat resistance, and strength make them a valuable addition to industries ranging from construction to food processing. Considering their long lifespan and environmental benefits, these pipes are indeed a wise investment.
FAQs
1. Are 316 stainless steel square pipes suitable for outdoor applications?
Yes, their corrosion resistance makes them ideal for outdoor use.
2. Can 316 stainless steel square pipes be painted or coated?
Yes, they can be painted or coated for added protection or aesthetics.
3. What is the typical lifespan of 316 stainless steel square pipes?
With proper maintenance, they can last for several decades.
4. Are there any limitations to welding 316 stainless steel?
While it can be welded, it requires proper equipment and expertise to maintain its corrosion resistance.
5. How does the cost of 316 stainless steel compare to other materials?
It is often more expensive upfront but offers long-term cost savings due to its durability.