Stainless steel is a versatile alloy renowned for its corrosion resistance and durability. Within the spectrum of stainless steel variants, two widely used types are 410 and 316 stainless steel. Understanding their properties, applications, and differences is crucial for various industries and applications.
Introduction to Stainless Steel
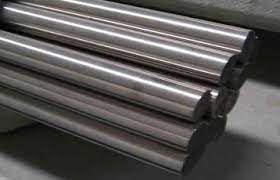
Stainless steel is a versatile and durable alloy that’s celebrated for its resistance to corrosion. It’s a type of steel alloy composed primarily of iron, carbon, and a minimum of 10.5% chromium. This high chromium content forms a protective layer on the steel’s surface, preventing rust and corrosion, which are common issues with other types of steel.
One of the key characteristics of stainless steel is its ability to withstand exposure to various environmental factors, including moisture, acids, and extreme temperatures, without losing its structural integrity. It’s widely appreciated for its strength, durability, and hygienic properties, making it a popular choice in numerous industries, including construction, automotive, healthcare, and manufacturing.
Understanding 410 Stainless Steel
Composition and Characteristics
When discussing the composition and characteristics of stainless steel, it’s important to highlight that stainless steel is primarily composed of iron, chromium, carbon, and varying amounts of other alloying elements like nickel, molybdenum, or manganese.
The percentage of chromium is a defining factor in stainless steel. This alloying element contributes significantly to the steel’s corrosion resistance by forming a thin, invisible oxide layer on the surface when exposed to oxygen. This layer, known as the passive layer, protects the steel from rust and corrosion, making it highly durable in various environments.
The carbon content in stainless steel varies but is generally kept relatively low compared to other types of steel, contributing to its strength and hardness. Other alloying elements like nickel and molybdenum enhance specific properties such as resistance to acids, high temperatures, or improving machinability.
The combination of these elements results in stainless steel’s exceptional strength, durability, and resistance to corrosion, making it a sought-after material across diverse industries for a wide range of applications.
Applications and Industries
- Construction: Stainless steel is widely used in construction for structural elements, facades, roofing, and interior design due to its durability, aesthetic appeal, and resistance to corrosion, even in harsh weather conditions.
- Automotive: In the automotive industry, stainless steel is utilized in exhaust systems, decorative trims, and structural components due to its heat resistance and ability to withstand exposure to road salts and moisture.
- Healthcare: It’s a critical material in the medical field for surgical instruments, medical devices, and equipment due to its hygienic properties, resistance to sterilization processes, and corrosion resistance in bodily fluids.
- Food and Beverage Industry: Stainless steel is prevalent in this industry for food processing equipment, storage tanks, and kitchen appliances due to its corrosion resistance, ease of cleaning, and non-reactivity with food substances.
- Oil and Gas: It’s used in pipelines, storage tanks, and offshore platforms due to its resistance to corrosive environments, high temperatures, and pressure.
- Maritime: Stainless steel, particularly grades like 316, is extensively used in marine applications for boat fittings, underwater equipment, and shipbuilding due to its superior resistance to saltwater corrosion.
Exploring 316 Stainless Steel
Composition and Features
- Composition: Stainless steel is primarily composed of iron, chromium, and often includes other elements like nickel, molybdenum, or manganese. The key component, chromium, typically constitutes at least 10.5% of its composition. This high chromium content is crucial as it forms a protective oxide layer on the surface of the steel, preventing corrosion and rust.
- Features:
- Corrosion Resistance: The formation of the chromium oxide layer provides stainless steel with exceptional resistance to corrosion, making it suitable for use in various environments, including those with high moisture or chemical exposure.
- Strength and Durability: Stainless steel exhibits remarkable strength and durability, making it ideal for structural applications where toughness and longevity are essential.
- Aesthetic Appeal: Its sleek appearance and ability to maintain its shine over time make stainless steel a popular choice for decorative and architectural purposes.
- Hygienic Properties: Stainless steel is non-porous, making it easy to clean and resistant to bacterial growth, which is why it’s extensively used in medical and food-related industries.
- Heat Resistance: Depending on the specific grade, stainless steel can withstand high temperatures, making it suitable for applications exposed to heat, such as in automotive exhaust systems or industrial furnaces.
Usage in Different Fields
- Medical and Healthcare: In the medical field, stainless steel is crucial for surgical instruments, implants, and medical devices due to its biocompatibility, corrosion resistance, and ease of sterilization.
- Food Processing and Catering: It’s prevalent in food-related industries for equipment like sinks, countertops, machinery, and utensils due to its hygiene, resistance to corrosion, and ease of cleaning.
- Architecture and Design: Stainless steel’s aesthetic appeal, durability, and resistance to weathering make it a favored material for architectural elements, such as facades, railings, and interior decor.
- Automotive and Transportation: Its use in automotive parts, such as exhaust systems, structural components, and decorative trims, is owing to its resistance to corrosion, heat, and mechanical strength.
- Maritime and Aerospace: Particularly grades like 316, stainless steel is preferred for its resistance to saltwater corrosion, making it essential in shipbuilding, marine fittings, and aerospace applications.
- Oil and Gas Industry: Stainless steel is used in pipelines, storage tanks, and valves due to its ability to withstand corrosive environments and high temperatures in oil refineries and processing plants.
- Construction and Infrastructure: It’s employed in construction for structural components, roofing, cladding, and reinforcement due to its strength, corrosion resistance, and aesthetic appeal.
Comparing 410 and 316 Stainless Steel
Mechanical Properties
- Strength: Stainless steel exhibits impressive strength, providing structural integrity and reliability in demanding environments. Its ability to withstand heavy loads and stresses makes it suitable for numerous industrial and structural applications.
- Hardness: Depending on the grade and treatment, stainless steel can achieve varying levels of hardness. Some variants, like 410 stainless steel, are notably harder, making them suitable for applications requiring resistance to abrasion and wear.
- Ductility: While stainless steel is generally strong, it also possesses a degree of ductility, allowing it to be shaped and formed into various shapes and configurations without losing its structural integrity.
- Toughness: Stainless steel demonstrates excellent toughness, enabling it to absorb energy and withstand impacts without fracturing or breaking easily. This property is crucial in applications subjected to sudden or repeated loads.
- Machinability: The machinability of stainless steel refers to its ease of being machined or shaped using cutting and drilling tools. Different grades exhibit varying degrees of machinability based on their composition and treatment processes.
Corrosion Resistance
- Passive Layer Formation: The key to stainless steel’s corrosion resistance lies in its ability to form a passive oxide layer on its surface when exposed to oxygen. This layer, primarily composed of chromium oxide, acts as a protective barrier, preventing direct contact between the steel and corrosive elements in the environment.
- Chromium Content: The high chromium content in stainless steel, typically a minimum of 10.5%, is crucial for the formation of this protective oxide layer. This layer is self-repairing, reforming if damaged, and continuously protecting the underlying steel.
- Resistance to Various Environments: Stainless steel exhibits exceptional resistance to corrosion from moisture, atmospheric conditions, chemicals, acids, and even certain alkaline solutions. Different grades of stainless steel offer varying levels of corrosion resistance, with specific alloys designed to withstand harsher environments.
- Pitting and Crevice Corrosion: Some grades of stainless steel, like 316, are particularly adept at resisting pitting and crevice corrosion, making them suitable for marine and chloride-rich environments where other metals might fail.
- Longevity and Durability: Due to its resistance to corrosion, stainless steel products tend to have a longer lifespan and require minimal maintenance, making them cost-effective solutions in various industries.
Strengths and Weaknesses
Strengths:
- Corrosion Resistance: Its primary advantage lies in its exceptional resistance to corrosion, making it suitable for various environments, including those with high moisture, chemicals, or salt exposure.
- Strength and Durability: Stainless steel is renowned for its strength, providing structural integrity in diverse applications. It’s durable, with the ability to withstand heavy loads and harsh conditions.
- Hygienic Properties: Its non-porous surface makes it easy to clean and sterilize, making it a preferred choice in industries requiring high hygiene standards, such as healthcare and food processing.
- Aesthetic Appeal: Stainless steel’s sleek and shiny appearance, along with its ability to maintain its luster over time, makes it a popular choice for architectural and decorative purposes.
Weaknesses:
- Cost: Certain grades of stainless steel, especially those with higher corrosion resistance or specialized properties, can be more expensive than other materials, impacting budget considerations.
- Lower Thermal Conductivity: Compared to some other metals, stainless steel has lower thermal conductivity, which might limit its suitability in certain high-temperature applications.
- Magnetic Properties: Some stainless steel grades are not magnetic, which can be a limitation in applications where magnetic properties are required.
- Specific Alloy Properties: Different grades of stainless steel offer various properties, and selecting the right grade for a specific application is crucial, as each might have limitations or strengths depending on the intended use.
410 vs 316 Stainless Steel: Factors Influencing Choice between 410 and 316
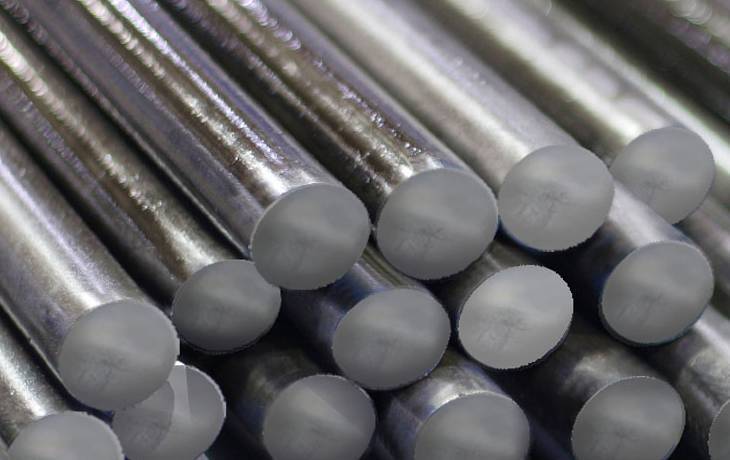
Environmental Conditions
- Moisture and Humidity: Stainless steel excels in environments with high moisture content. Its corrosion resistance makes it an excellent choice for outdoor applications, coastal regions, or places prone to humidity.
- Chemical Exposure: It’s resistant to a wide range of chemicals, acids, and alkalis, making it suitable for industries dealing with corrosive substances such as laboratories, chemical processing plants, and the pharmaceutical industry.
- Temperature Extremes: Stainless steel maintains its integrity at both high and low temperatures, making it valuable in applications exposed to extreme heat or cold, such as in industrial furnaces or cryogenic applications.
- Chloride-Rich Environments: Grades like 316 stainless steel are highly resistant to chloride corrosion, making them ideal for marine environments, swimming pools, or areas exposed to salt sprays.
- Pollution and Urban Settings: Stainless steel’s durability and resistance to atmospheric pollutants make it an excellent choice for urban infrastructure, where exposure to pollutants and environmental contaminants is common.
- Bacterial and Fungal Resistance: Its non-porous surface inhibits bacterial growth, making it suitable for hygiene-sensitive environments like hospitals, food processing, and pharmaceutical facilities.
Specific Applications
- Medical Equipment: Surgical instruments, implants, and medical devices rely on stainless steel due to its biocompatibility, corrosion resistance, and sterilization capabilities.
- Food Processing: Equipment like storage tanks, conveyor belts, and food preparation surfaces utilize stainless steel for its hygiene, corrosion resistance, and ease of cleaning, ensuring food safety standards.
- Architectural Design: Stainless steel finds its place in architectural elements such as facades, railings, sculptures, and interior decor due to its aesthetic appeal, durability, and resistance to weathering.
- Automotive Parts: Exhaust systems, decorative trims, and structural components benefit from stainless steel’s corrosion resistance, heat tolerance, and durability in the automotive industry.
- Marine Applications: Shipbuilding, boat fittings, and marine equipment utilize stainless steel, especially grade 316, for its superior resistance to saltwater corrosion.
- Chemical Processing: Stainless steel’s resistance to chemical corrosion makes it valuable in chemical processing plants for storage tanks, pipelines, and equipment handling corrosive substances.
- Construction and Infrastructure: In construction, stainless steel is used for structural components, roofing, cladding, and reinforcement due to its strength, durability, and aesthetic appeal.
- Oil and Gas Industry: Stainless steel plays a role in the oil and gas sector for pipelines, storage tanks, and valves due to its resistance to corrosive environments and high temperatures.
Cost Considerations
- Initial Cost: The initial cost of stainless steel can vary based on the grade, finish, and specific properties required for the application. Higher grades with enhanced corrosion resistance or specialized characteristics might incur higher initial expenses.
- Long-Term Investment: While stainless steel might have a higher upfront cost compared to other materials, its durability and longevity often result in lower maintenance and replacement expenses over its lifecycle. This can make it a cost-effective long-term investment.
- Grade Selection: Different grades of stainless steel come with varying costs. For instance, 316 stainless steel, known for its exceptional corrosion resistance, might be more expensive than 304 stainless steel, which is more commonly used but with slightly lower corrosion resistance.
- Application Specifics: The specific requirements of the application influence the cost. For applications where corrosion resistance, hygiene, or durability are critical, opting for higher-grade stainless steel might be necessary, impacting the overall cost.
- Fabrication and Installation: The cost of fabricating and installing stainless steel components also contributes to the overall expenses. Precision cutting, welding, and installation processes may increase the overall project cost.
- Maintenance and Lifespan: Stainless steel’s minimal maintenance requirements and longer lifespan compared to other materials can offset higher initial costs by reducing ongoing maintenance expenses and the need for frequent replacements.
Practical Applications and Recommendations
- High Corrosion Environments: In settings where corrosion is a concern, especially in marine or coastal areas, choosing higher-grade stainless steel like 316 or duplex stainless steel is recommended due to their superior corrosion resistance.
- Structural Components: For structural applications requiring strength and durability, grades like 304 or 316 stainless steel are suitable due to their robust mechanical properties, ensuring structural integrity.
- Hygienic Environments: Industries like healthcare, food processing, and pharmaceuticals benefit from stainless steel’s hygienic properties. Using grades like 316L with a smoother finish can further enhance its cleanliness and resistance to bacterial growth.
- High-Temperature Environments: For applications exposed to high temperatures, selecting heat-resistant grades like 310 or 321 stainless steel is advisable to maintain structural stability and corrosion resistance.
- Cost-Effective Solutions: When cost is a significant factor, utilizing lower-cost stainless steel grades such as 430 or 409, which offer moderate corrosion resistance and strength, can be a practical solution for certain applications.
- Design and Aesthetics: Stainless steel’s aesthetic appeal makes it a preferred choice for architectural and decorative purposes. Various finishes, such as brushed, polished, or textured, allow for versatile design options.
- Maintenance Considerations: Regular cleaning and maintenance can prolong the lifespan of stainless steel components. Choosing the appropriate grade based on the required maintenance level can streamline upkeep efforts.
- Consultation with Experts: Consulting with metallurgical experts or stainless steel suppliers can provide valuable insights into selecting the right grade, finish, and fabrication techniques for specific applications.
Conclusion
In conclusion, the choice between 410 and 316 stainless steel depends on various factors, including mechanical requirements, environmental conditions, and budget considerations. Each type has its strengths and weaknesses, catering to specific applications across diverse industries.
FAQs
- Which stainless steel is better for marine applications?
- 316 stainless steel is preferred due to its superior corrosion resistance in marine environments.
- What makes 410 stainless steel stand out?
- 410 steel excels in mechanical strength and hardness, suitable for applications prioritizing these properties.
- Is 316 stainless steel more expensive than 410?
- Yes, typically, 316 stainless steel is more expensive due to its additional alloying elements.
- Can 410 stainless steel be used in chemical processing?
- It can be used but might not provide the same corrosion resistance as 316 steel in such environments.
- In what applications does 410 stainless steel find significant use?
- It’s commonly used in valves, pumps, and various industrial components where strength is crucial.