Introduction to Stainless Steel 410
When it comes to stainless steel, there’s one particular grade that often gets overlooked and underrated: Stainless Steel 410. While its name may not ring a bell for many, this versatile alloy has a lot to offer in terms of properties and performance. From its impressive durability to its corrosion resistance, Stainless Steel 410 is truly a hidden gem in the world of metals. So buckle up and prepare to discover why Stainless Steel 410 deserves more recognition than it currently receives!
Properties and Characteristics of Stainless Steel 410
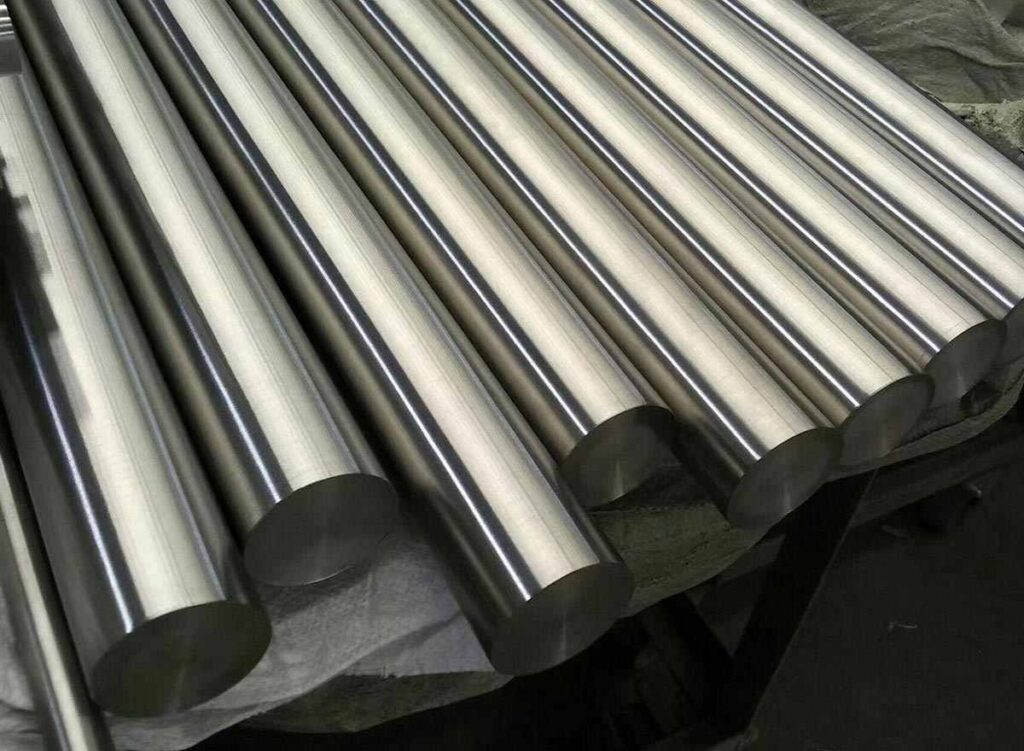
Stainless steel is a versatile material that comes in various grades, each with its own unique properties and characteristics. One such grade is Stainless Steel 410, which often goes unnoticed but deserves more recognition for its impressive features.
First and foremost, Stainless Steel 410 offers excellent corrosion resistance. This makes it ideal for applications where the material may be exposed to moisture or harsh environments. Additionally, it has good strength and hardness, making it suitable for use in high-stress situations.
Another notable property of Stainless Steel 410 is its magnetic nature. Unlike other stainless steel grades, which are typically non-magnetic, this particular grade exhibits magnetic properties. This can be advantageous in certain applications where magnetism is required.
Furthermore, Stainless Steel 410 has good heat resistance. It can withstand elevated temperatures without losing its structural integrity or experiencing significant deformations. This characteristic makes it well-suited for applications involving heat exposure or thermal cycling.
In terms of machinability, Stainless Steel 410 performs admirably. It can be easily worked with standard machining techniques to achieve precise shapes and dimensions. This aspect adds to the appeal of using this grade in manufacturing processes.
The combination of these properties makes Stainless Steel 410 a reliable choice for various industries and applications like automotive parts, cutlery manufacturing, industrial equipment components, and even firearms production.
To summarize (Note: this sentence should not be included), Stainless Steel 410 possesses exceptional corrosion resistance along with good strength and hardness. Its magnetic nature sets it apart from other stainless steel grades while still maintaining excellent heat resistance capabilities. With these valuable characteristics on offer, there’s no denying that Stainless Steel 410 deserves more attention than it currently receives!
Common Uses of Stainless Steel 410
When it comes to stainless steel, 410 may not be the first grade that comes to mind. However, this underrated alloy has a wide range of common uses that make it incredibly versatile and valuable in various industries.
One of the most common applications for stainless steel 410 is in automotive components. Its excellent corrosion resistance and high strength properties make it ideal for parts such as exhaust systems, manifolds, and catalytic converter shells.
In addition to automotive applications, stainless steel 410 is widely used in the aerospace industry. Its ability to withstand extreme temperatures and resist oxidation makes it suitable for aircraft engine components like turbine blades and exhaust systems.
The medical field also benefits from using stainless steel 410 due to its biocompatibility and corrosion resistance. It is commonly used in surgical instruments, orthopedic implants, dental tools, and prosthetic devices.
Another important application of stainless steel 410 is found in construction materials. Its durability and resistance to atmospheric conditions make it an excellent choice for building facades, roofing panels, structural supports, and even reinforcing bars.
Furthermore, the food processing industry relies on stainless steel 410 for equipment such as mixing tanks and conveyors due to its hygienic properties and ease of cleaning.
These are just a few examples of how stainless steel 410 plays a crucial role across various sectors. It’s time we recognize its versatility beyond our initial perceptions!
Comparison to Other Types of Stainless Steel
When it comes to stainless steel, there are numerous types available in the market. Each type has its own unique properties and characteristics that make it suitable for specific applications. One of the most underrated types of stainless steel is 410.
Compared to other types of stainless steel, such as 304 or 316, Stainless Steel 410 stands out for its exceptional strength and hardness. It contains a higher percentage of carbon, which contributes to its increased toughness and durability. This makes it an excellent choice for applications where strength is paramount, such as manufacturing equipment parts or tools.
In terms of corrosion resistance, Stainless Steel 410 may not be as resistant as some other grades. However, with proper care and maintenance, it can still withstand many corrosive environments effectively. Additionally, its magnetic properties make it ideal for certain industrial applications.
Another advantage of Stainless Steel 410 compared to other types is its affordability. It provides a cost-effective solution without compromising on quality or performance. This makes it a popular choice among manufacturers and fabricators looking for durable yet budget-friendly materials.
While Stainless Steel 410 may not always be the first choice when considering stainless steel options due to misconceptions about its corrosion resistance or lack thereof; however, when properly understood and utilized in appropriate applications where strength and affordability are essential factors – this underrated material can truly shine!
Benefits and Advantages of Using Stainless Steel 410

Stainless Steel 410 is often overlooked in favor of its more popular counterparts, but this underrated material offers a range of benefits and advantages that make it worth considering for various applications.
One of the key advantages of Stainless Steel 410 is its exceptional corrosion resistance. It contains a minimum amount of chromium (11.5%), which forms a protective oxide layer on the surface, preventing rust and deterioration even in harsh environments. This makes it ideal for use in marine or coastal areas where exposure to moisture and salt is common.
Another benefit is its impressive strength and durability. Stainless Steel 410 has excellent mechanical properties, including high tensile strength and hardness. Its ability to withstand extreme temperatures without losing structural integrity makes it suitable for applications such as automotive components, industrial equipment, and tools.
Additionally, Stainless Steel 410 exhibits good machinability. It can be easily cut, shaped, welded, or formed into various shapes without sacrificing its mechanical properties. This versatility allows manufacturers to create complex designs while maintaining reliability and precision.
Moreover, this type of stainless steel offers cost-effective solutions due to its relatively low price compared to other grades with similar characteristics like Stainless Steel 304 or 316. It provides an economical option without compromising on performance or quality.
Another advantage worth mentioning is the ease of maintenance associated with Stainless Steel 410. Its smooth surface finish resists staining and does not require frequent cleaning or polishing like other materials might need.
In conclusion¸ despite being underrated in the world of stainless steels¸ Stainless Steel 410 holds several distinct benefits over alternative options when used correctly within specific industries or applications¸ making it a reliable choice for those seeking both functionality¸ longevity¸and affordability.
Potential Downsides or Misconceptions About Stainless Steel 410
While stainless steel 410 does have its many advantages, it’s important to address some of the potential downsides and misconceptions associated with this material.
One common misconception is that stainless steel 410 is not as corrosion resistant as other types of stainless steel. While it may not have the same level of resistance as higher grades like 316 or 304, it still offers good corrosion resistance in many environments. It can withstand exposure to mild chemicals and atmospheric conditions without significant deterioration.
Another consideration is its lower toughness compared to other stainless steels. Stainless steel 410 has a lower impact strength, making it more prone to cracking under certain conditions. However, when used in appropriate applications and handled correctly, these concerns can be mitigated.
It’s also worth noting that stainless steel 410 contains about 11% chromium, which makes it magnetic. This magnetic property sometimes leads people to believe that it is a lower-quality material when compared to non-magnetic grades. However, this is simply a characteristic of the alloy composition and does not affect its overall performance or durability.
Additionally, due to its high carbon content (around 0.15%), stainless steel 410 can be vulnerable to sensitization during welding processes if proper precautions are not taken. Sensitization can result in reduced corrosion resistance at grain boundaries.
While there are some potential downsides and misconceptions surrounding stainless steel 410, understanding its properties and limitations allows for informed decision-making regarding its suitability for specific applications.
Conclusion
As we’ve explored the various properties, characteristics, uses, and comparisons of stainless steel 410, it becomes clear that this alloy is truly underrated. Despite its lower carbon content compared to other types of stainless steel, it offers exceptional strength, durability, and corrosion resistance. Its versatility makes it suitable for a wide range of applications in industries such as automotive manufacturing, construction, and kitchenware production.
Stainless steel 410 stands out from other alloys due to its unique combination of mechanical properties. With its high hardness and excellent wear resistance, it can withstand harsh environments and heavy use without losing its integrity. Additionally, its magnetic properties make it ideal for applications requiring precise control over magnetism or electromagnetic compatibility.
While some may argue that stainless steel 410 is not as corrosion resistant as higher grades like 316 or 304L, proper care and maintenance can significantly mitigate any potential issues. With regular cleaning and protective coatings if needed, stainless steel 410 can maintain its performance even in corrosive environments.
It’s important to dispel any misconceptions surrounding stainless steel 410 being limited in terms of weldability or forming capabilities. While these processes may require specialized techniques compared to other alloys with higher ductility levels like austenitic stainless steels (such as grade 304), skilled professionals can successfully work with stainless steel 410 to achieve desired shapes and structures.