430 Stainless Steel vs 316: Unveiling the Ideal Alloy for Your Needs.Stainless steel is a versatile and crucial material used across numerous industries due to its durability, corrosion resistance, and aesthetic appeal. However, not all stainless steel is created equal. Two popular grades, 430 and 316, stand out with their unique properties and applications.
Introduction to Stainless Steel Grades
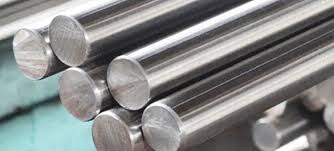
Stainless steel alloys are a composite of iron, carbon, and varying amounts of elements like chromium, nickel, and manganese. These alloys are categorized into different grades based on their composition and properties, with each grade designed for specific applications.
Understanding 430 Stainless Steel
430 stainless steel is a ferritic, straight chromium alloy known for its excellent corrosion resistance in mildly corrosive environments. Composed of 17% chromium and 0.12% carbon, it finds applications in kitchen appliances, automotive trim, and architectural applications due to its attractive appearance and ease of fabrication. However, it might lack the robustness needed in highly corrosive settings.
Exploring 316 Stainless Steel
In contrast, 316 stainless steel, an austenitic alloy with 10% nickel and 2% molybdenum, exhibits superior corrosion resistance, making it ideal for marine environments, chemical processing, and medical devices. Its increased nickel content enhances its resistance to corrosion and oxidation, offering durability in harsh conditions.
Comparison between 430 and 316 Stainless Steel
When comparing these two alloys, their corrosion resistance, mechanical properties, and cost-effectiveness are pivotal factors. While 430 stainless steel excels in non-corrosive settings and is more affordable, 316 stainless steel surpasses it in resisting corrosion, making it suitable for harsh environments despite being more expensive.
Characteristics | 430 Stainless Steel | 316 Stainless Steel |
---|---|---|
Composition | 17% chromium, 0.12% carbon | 16-18% chromium, 10-14% nickel, 2% molybdenum |
Corrosion Resistance | Good in mildly corrosive environments | Excellent, particularly in aggressive environments |
Strength | Moderate strength | Stronger and more durable |
Magnetic Properties | Magnetic due to its ferritic structure | Non-magnetic in annealed condition |
Applications | Kitchen appliances, automotive trim, architectural use | Marine environments, chemical processing, medical devices |
Cost | More affordable | Relatively more expensive |
Resistance to Chlorides | Vulnerable to chloride corrosion | Highly resistant to chloride corrosion |
Temperature Resistance | Susceptible to high temperatures | Maintains strength at high temperatures |
Weldability | Easily welded | Requires expertise for welding |
Appearance | Attractive and glossy | Polished, high-quality appearance |
Factors Influencing Choice
Deciding between these alloys hinges on specific applications, environmental conditions, and budget considerations. For environments with high chloride exposure or extreme temperatures, 316 stainless steel might be the optimal choice despite its higher cost.
Real-world Examples
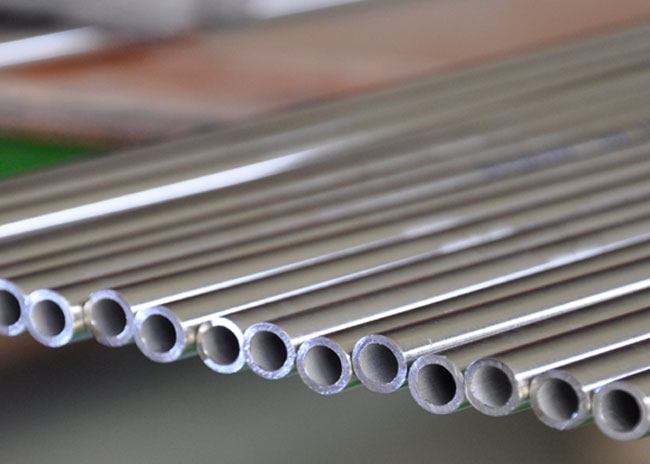
In the automotive industry, 430 stainless steel might suffice for non-exposed components, whereas 316 stainless steel becomes imperative for parts subjected to salt exposure, like marine components or coastal infrastructure.
Future Trends in Stainless Steel Selection
As technology advances, innovations in stainless steel production aim to enhance both the performance and cost-effectiveness of these alloys. The industry continues to witness demands for more sustainable, corrosion-resistant materials, driving research and development for newer stainless steel grades.
Conclusion
In conclusion, while both 430 and 316 stainless steel offer unique advantages, the choice ultimately rests on the specific requirements of the application. Understanding their properties and considering environmental factors and budget constraints are essential in making an informed decision.
FAQs
Which stainless steel is better for outdoor applications?
- Typically, 316 stainless steel performs better due to its higher corrosion resistance, ideal for outdoor exposure.
Is 430 stainless steel magnetic?
- Yes, 430 stainless steel is magnetic due to its ferritic structure.
Can I use 316 stainless steel in contact with food?
- Yes, 316 stainless steel is commonly used in food processing equipment due to its corrosion resistance and non-reactive nature.
What is the main difference between 430 and 316 stainless steel?
- The primary difference lies in their corrosion resistance and composition. 316 stainless steel offers superior corrosion resistance due to its nickel and molybdenum content.
Which grade is more cost-effective?
- Generally, 430 stainless steel is more cost-effective than 316 stainless steel, but the choice depends on the specific application’s requirements.