Introduction to 430 and 304 Stainless Steel
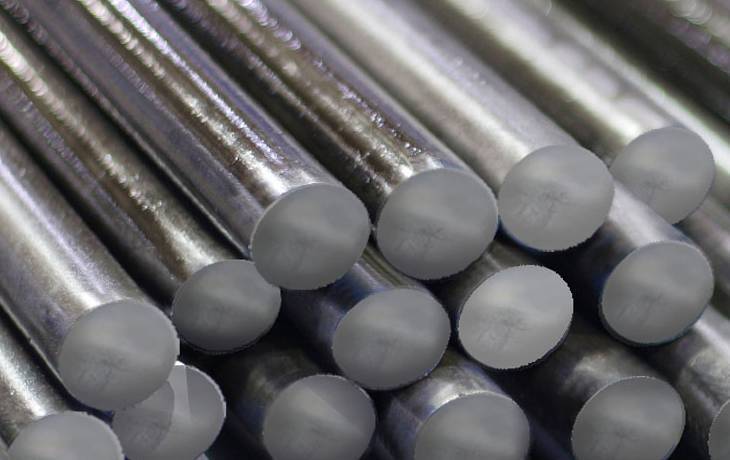
Stainless steel 430 and 304 are two of the most commonly used stainless steel grades. Stainless steel in general provides excellent corrosion resistance, durability, and low maintenance when compared to other metals. Within the stainless steel family, different grades offer various properties based on their chemical composition and microstructure.
Stainless steel 430 has a higher chromium content than 304, providing good corrosion resistance properties. 304 stainless steel has a higher nickel content, facilitating greater durability and tensile strength. Understanding key differences and characteristics between 430 and 304 can help determine which is better suited for any given application.
Composition Comparison
The composition of stainless steel 430 and 304 differs primarily in their nickel, manganese, silicon, and carbon content. Here is a helpful composition comparison:
Alloy | Chromium | Nickel | Manganese | Silicon | Carbon |
---|---|---|---|---|---|
430 | 16-18% | 0.12% max | 1.0% max | 1.0% max | 0.12% max |
304 | 18-20% | 8-10.5% | 2% max | 0.75% max | 0.08% max |
The higher chromium content in 430 enhances corrosion resistance given chromium forms a protective surface oxide layer. The increased nickel content in 304 boosts durability and tensile properties. The manganese and silicon increases 304’s resistance to various forms of chemical corrosion. The lower carbon content ensures 304 is highly weldable.
Corrosion Resistance
While both offer substantial corrosion resistance, 304 generally provides better overall performance. The added nickel gives 304 higher resistance to caustic corrosion,environments with sulfuric, tartaric, and citric acid. Stainless steel 430’s higher chromium but lack of nickel limits certain chemical corrosion resistance.
However, stainless steel 430’s higher chromium does afford greater resistance to alkaline solutions as well as sodium sulfate. And its lower nickel eliminates susceptibility to highly aggressive halogen salts environments. Determining the necessary degree of chemical corrosion resistance factors greatly in choosing between 430 and 304.
Heat Resistance and Scaling Behavior
Stainless steel 304 offers moderately better heat resistance properties, alongside lower risk of scaling at high temperatures when compared to 430 stainless steel. 304 can effectively handle temperatures ranging from -50 to 870°C for intermittent exposure, in contrast to 430 stainless steel’s range of -50 to 760°C.
Additionally, 430’s lower chromium-to-nickel ratio heightens risk of carbide precipitation at high welding temperatures over 500°C which can form thick, coarse grain carbides. This makes it more susceptible to embrittlement and intergranular corrosion. 304 resists embrittlement and can better endure repeated heating and cooling cycles making it preferable for high temperature applications.
Fabrication Characteristics
304 stainless steel exhibits better fabrication properties than 430 when shaped and joined. Its lower carbon content coupled with the nickel addition enables excellent weldability and formability when hot worked. This allows 304 to handle very high plastic deformation operations like deep drawing when making sinks, cookware, and cups.
430 stainless steel’s hardness can lead to cracking during severe fabrication procedures requiring intense bending or drawing. Machinability and grinding is also more difficult. However, 430’s hardness does lend itself well to applications needing high rigidity like oven liner trays, utensils, and dental and medical tools.
Typical Applications
Stainless Steel 430
- Architecture fixtures and hardware
- Automotive trim parts
- Dental and medical instruments
- Kitchen appliances
- Kitchen utensils and cookware
Stainless Steel 304
- Architecture panels, railings, trim
- Food processing and pharmaceutical equipment
- Chemical and petrochemical production vessels
- Heat exchangers, boilers, and heaters
- Kitchen counters, sinks, appliances
As shown above, both find utility spanning consumer products to heavy industry. In general, 304 suits more fabricated parts and corrosive environments while 430 fits higher temperature, rigid uses.
Cost Comparison
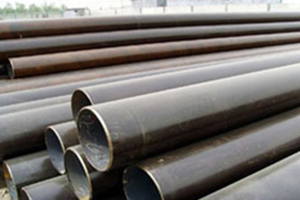
Stainless steel 430 generally has lower market pricing over 304 stainless steel. This mainly comes down to 304’s nickel content requiring more raw material costs. Current pricing averages:
- 430 stainless steel – $1.45/lb
- 304 stainless steel – $2.50/lb
So all characteristics equal, 430 should be chosen for cost saving reasons alone. However, 304’s superior longevity, versatility, and performance justify the cost increase for many critical applications.
Conclusion:Stainless Steel 430 Vs 304
When deciding between stainless steel 430 and 304 grades, consider factors of chemical and heat resistance needs, fabrication requirements, pricing, and application specifications that determine which allowance best suits performance goals. Quick comparison recap:
- Corrosion Protection – 304 superior for wide chemical types
- Heat Scaling Resistance – 304 resists better for severe cycling
- Fabrication Capability – 304 enables more extreme forming
- Cost Factors – 430 less expensive per pound in raw state
- Common Uses – 430 for high temperature rigid uses, 304 for fabricated corrosive environment parts
For questions on selecting an optimal stainless steel type and heat treatment for a specific application, consult a metallurgical engineer to ensure all structural needs and criteria are met.
FAQs
Q: Which stainless steel is magnetic, 430 or 304?
A: Stainless steel 430 is magnetic in all conditions given its body-centered cubic crystal structure. 304 stainless steel is only magnetic after heavy cold working that distorts its normal face-centered cubic austenitic structure. In annealed form, 304 is non-magnetic.
Q: Is 430 stainless steel brittle or ductile?
A: 430 stainless steel does have lower notch ductility than 304, but still exhibits at least 20-25% elongation and reduction of area, classifying it as a ductile material rather than a brittle one. Proper heat treatment ensures a sufficiently ductile state for fabrication.
Q: Can 430 stainless steel be welded?
A: Yes, 430 stainless steel can be welded, but it has a higher risk of chromium-carbide precipitation and reduced corrosion resistance in heat affected zones, requiring greater care than 304. Low heat input TIG welding is easiest, but other processes work with proper procedures following.
Q: What is the difference between 409 and 430 stainless steel?
A: The main difference is that 409 stainless steel has a much lower chromium content of 10.5 to 11.5% which greatly reduces corrosion resistance compared to 430 stainless steel’s 16 to 18% chromium allowance. This makes 409 more prone to exterior rust damage.