Introduction
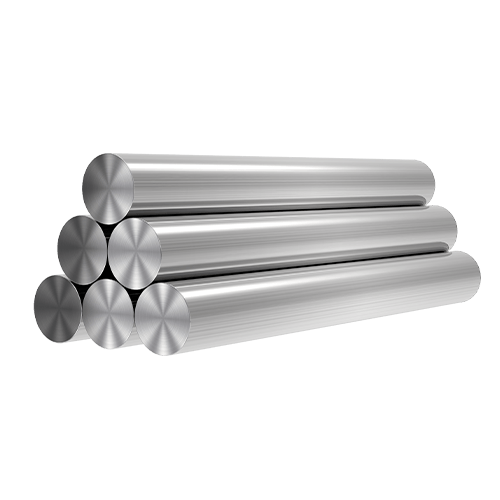
In the realm of materials engineering, 316 stainless steel pipes stand out for their exceptional corrosion resistance properties. Understanding the factors contributing to this resistance is crucial for various industries, from chemical processing to marine applications. In this comprehensive exploration, we delve into the mechanisms behind the corrosion resistance of 316 stainless steel pipes, shedding light on their durability and reliability.
The Chemistry Behind 316 Stainless Steel Pipes
The chemistry behind 316 stainless steel pipes is a fascinating blend of carefully chosen elements and their interactions, resulting in remarkable corrosion resistance properties. Let’s delve deeper into the intricacies of this alloy composition:
Chromium: Chromium is the primary element responsible for the corrosion resistance of stainless steel. In 316 stainless steel, chromium content typically ranges between 16-18%. When exposed to oxygen, chromium reacts to form a thin, invisible oxide layer on the surface of the steel. This oxide layer, known as the passive film, acts as a protective barrier against corrosion by preventing further oxidation of the underlying metal.
Molybdenum: Molybdenum is another crucial alloying element in 316 stainless steel, typically present in concentrations of 2-3%. Molybdenum enhances the corrosion resistance of the steel, especially in chloride-rich environments such as seawater and industrial atmospheres. It helps to stabilize the passive film formed by chromium, making it more resistant to pitting corrosion and localized attacks.
Nickel: Nickel plays a vital role in improving the overall corrosion resistance and mechanical properties of 316 stainless steel. With a nickel content of around 10-14%, this alloy exhibits excellent toughness, ductility, and resistance to stress corrosion cracking. Nickel also contributes to the stability of the austenitic structure, ensuring the material retains its strength and integrity even at elevated temperatures.
Passive Film Formation: The synergy between chromium, molybdenum, and nickel facilitates the formation of a stable and adherent passive film on the surface of 316 stainless steel pipes. This passive film is typically composed of chromium oxide (Cr2O3) and a small amount of other metal oxides. It acts as a physical barrier, preventing corrosive species such as oxygen, water, and chlorides from reaching the underlying metal surface.
Mechanisms of Corrosion Protection
The corrosion resistance of 316 stainless steel pipes stems from both intrinsic and extrinsic factors. The presence of chromium promotes the formation of a chromium oxide layer, which acts as a barrier against corrosion. Additionally, the alloy’s microstructure, characterized by austenitic crystalline phase, enhances its resistance to pitting and crevice corrosion.
Environmental Considerations
While 316 stainless steel pipes excel in a wide range of environments, certain factors can compromise their corrosion resistance. Exposure to chloride ions, extreme temperatures, and acidic solutions may accelerate corrosion processes, necessitating proactive measures such as surface treatments or alloy modifications.
Case Studies and Performance Evaluation
Real-world applications provide invaluable insights into the corrosion resistance of 316 stainless steel pipes. Case studies across industries showcase the material’s performance in diverse settings, from offshore oil rigs to pharmaceutical manufacturing plants. Through rigorous testing and analysis, engineers continually refine their understanding of corrosion mechanisms, driving innovation in material design and fabrication.
Analyzing Corrosion Data
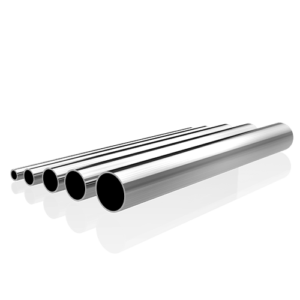
Environment | Corrosion Rate (mm/year) | Failure Mode |
---|---|---|
Marine Exposure | 0.05 | Pitting Corrosion |
Chemical Processing | 0.10 | Crevice Corrosion |
High Temperature | 0.08 | Oxidation |
Conclusion
The corrosion resistance of 316 stainless steel pipes is not merely a product of their chemical composition but a result of intricate interplays between alloy design, environmental factors, and surface conditions. By unraveling these complexities, engineers empower themselves to optimize material selection, mitigate corrosion risks, and ensure the longevity of critical infrastructure across industries.
FAQ
Q: Are 316 stainless steel pipes suitable for use in highly acidic environments?
A: Yes, thanks to their high chromium and nickel content, 316 stainless steel pipes exhibit excellent resistance to corrosion in acidic solutions, including sulfuric acid and hydrochloric acid.
Q: How do 316 stainless steel pipes compare to other stainless steel grades in terms of corrosion resistance?
A: While 316 stainless steel offers superior corrosion resistance compared to many other stainless steel grades, it may not be the most suitable choice for every application. Factors such as cost, mechanical properties, and specific environmental conditions must be considered when selecting the appropriate material.
Q: Can 316 stainless steel pipes withstand high temperatures?
A: Yes, 316 stainless steel pipes have a high melting point and can withstand elevated temperatures, making them suitable for applications involving heat transfer and processing.
Q: How can I maintain the corrosion resistance of 316 stainless steel pipes in harsh environments?
A: Regular inspection, proper surface cleaning, and the application of protective coatings can help preserve the corrosion resistance of 316 stainless steel pipes in challenging environments. Additionally, avoiding prolonged exposure to corrosive agents and maintaining optimal operating conditions are essential for prolonging the lifespan of the material.