Introduction
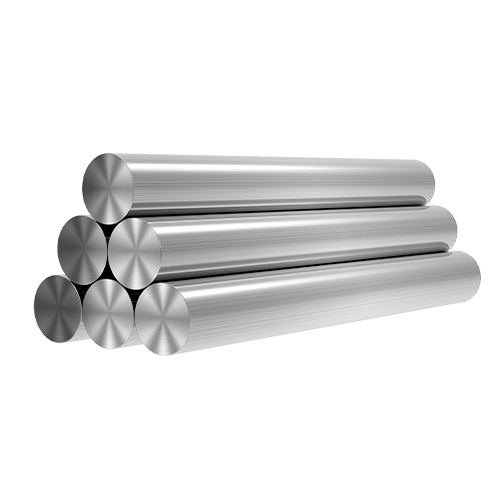
Stainless steel has long been lauded for its corrosion resistance properties, making it a popular choice in various industries. Among the different grades of stainless steel, 303 stainless steel tubing stands out for its unique composition and corrosion-resistant characteristics. In this blog post, we delve into the corrosion resistance of 303 stainless steel tubing, exploring its composition, applications, and factors influencing its resistance to corrosion.
Composition of 303 Stainless Steel Tubing
303 stainless steel tubing is renowned for its unique composition, which sets it apart from other grades such as the widely used 304 stainless steel. Its distinctive blend of elements contributes to its exceptional machinability and corrosion resistance.
Chromium, a key component in stainless steel alloys, constitutes a significant portion of 303 stainless steel tubing’s composition. Typically ranging from 17% to 19%, chromium forms a protective oxide layer on the surface of the steel when exposed to oxygen. This passive film acts as a barrier, shielding the underlying material from corrosion caused by environmental factors like moisture and chemicals.
In addition to chromium, nickel is another essential alloying element in 303 stainless steel tubing. Comprising approximately 8% to 10% of the alloy, nickel enhances the steel’s resistance to corrosion and oxidation, particularly in harsh conditions. This addition of nickel ensures that the tubing maintains its structural integrity and aesthetic appeal over an extended period.
One distinctive feature of 303 stainless steel tubing is its sulfur content, which distinguishes it from other stainless steel grades. Sulfur, present in quantities ranging from 0.15% to 0.35%, is deliberately added to improve machinability. The inclusion of sulfur promotes the formation of manganese sulfides, which act as chip breakers during machining processes, resulting in smoother and more efficient machining operations.
Furthermore, phosphorus and manganese are minor alloying elements in 303 stainless steel tubing, contributing to its overall performance. Phosphorus, typically present in amounts ranging from 0.20% to 0.60%, aids in enhancing the steel’s strength and corrosion resistance. Manganese, found in concentrations of up to 2%, facilitates the formation of a stable austenitic microstructure, further enhancing the tubing’s mechanical properties.
The synergistic combination of these elements results in a stainless steel alloy that excels in both machinability and corrosion resistance. Manufacturers and engineers favor 303 stainless steel tubing for applications where intricate machining operations are required without compromising on the material’s ability to withstand corrosive environments. Whether used in automotive components, medical devices, or aerospace applications, 303 stainless steel tubing offers a compelling blend of performance and versatility.
Corrosion Resistance Properties
303 stainless steel tubing exhibits excellent corrosion resistance in mild environments. Its high chromium content forms a passive oxide layer on the surface, providing protection against corrosion from moisture, oxygen, and other environmental factors. However, its sulfur content, which enhances machinability, can compromise its corrosion resistance in certain aggressive environments, such as chloride-rich or acidic conditions.
Factors Influencing Corrosion Resistance
Several factors influence the corrosion resistance of 303 stainless steel tubing:
- Environment: The type and aggressiveness of the environment significantly impact the corrosion rate. Mild environments typically pose minimal risk, while exposure to chlorides, acids, or high temperatures can accelerate corrosion.
- Surface Finish: A smooth surface finish reduces the likelihood of corrosion by minimizing crevices where corrosive agents can accumulate.
- Temperature: Elevated temperatures can exacerbate corrosion processes, especially in the presence of corrosive substances.
- Exposure Duration: Prolonged exposure to corrosive environments increases the likelihood of corrosion, especially if protective oxide layers are compromised.
Applications of 303 Stainless Steel Tubing
303 stainless steel tubing finds application in various industries, including:
- Automotive: Used in automotive components such as shafts, bushings, and fittings due to its corrosion resistance and machinability.
- Medical: Commonly employed in medical devices and equipment requiring both corrosion resistance and biocompatibility.
- Aerospace: Utilized in aircraft components subject to corrosive environments, such as fuel systems and hydraulic fittings.
- Manufacturing: Widely used in general manufacturing processes, particularly for machined components where both corrosion resistance and machinability are critical.
Characteristics of 303 stainless steel pipe:
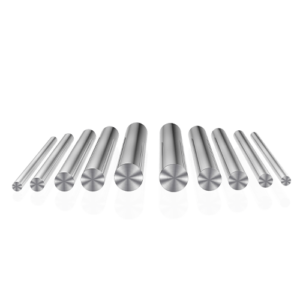
Property | Description |
---|---|
Density | 8.03 g/cm³ (at 20°C) |
Melting Point | 1455-1500°C |
Tensile Strength | 515 MPa (74,900 psi) |
Yield Strength | 205 MPa (29,700 psi) |
Elongation | 35% (in 50 mm) |
Modulus of Elasticity | 193 GPa (28 x 10^6 psi) |
Hardness (Brinell) | 262 (in annealed condition) |
Electrical Conductivity | 2.5% IACS (International Annealed Copper Standard) |
Conclusion
303 stainless steel tubing offers a balance of corrosion resistance and machinability, making it suitable for various applications across different industries. While its sulfur content enhances machinability, proper consideration of environmental factors is essential to ensure optimal corrosion resistance. By understanding its composition, properties, and influencing factors, manufacturers and engineers can effectively leverage 303 stainless steel tubing in diverse applications.
FAQ
Q:Is 303 stainless steel tubing suitable for marine environments?
A:While 303 stainless steel offers good corrosion resistance in mild marine environments, it may not be the best choice for prolonged exposure to seawater due to its sulfur content.
Q:Can 303 stainless steel tubing be welded?
A:Yes, 303 stainless steel tubing can be welded using common welding techniques. However, post-weld annealing may be required to restore corrosion resistance in the heat-affected zones.
Q:What is the difference between 303 and 304 stainless steel tubing?
A:303 stainless steel contains added sulfur for improved machinability, whereas 304 stainless steel does not. Additionally, 304 stainless steel typically has higher nickel content, providing superior corrosion resistance in certain environments.
Q:How can I maintain the corrosion resistance of 303 stainless steel tubing?
A:Regular cleaning and maintenance, avoiding exposure to harsh chemicals or environments, and ensuring proper surface finishing can help preserve the corrosion resistance of 303 stainless steel tubing.