Introduction
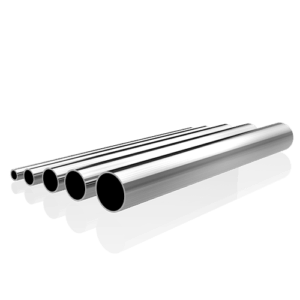
In the realm of industrial applications, the choice of materials is critical to ensuring performance, safety, and longevity. Stainless tubing stands out as a superior option due to its exceptional properties and versatility. From chemical processing to aerospace, stainless tubing offers a range of benefits that make it an ideal choice for various applications. This blog will delve into the top benefits of using stainless tubing in industrial settings, exploring its properties, applications, and advantages.
What is Stainless Tubing?
Stainless tubing is a type of tubular product made from stainless steel, a corrosion-resistant alloy primarily composed of iron, chromium, and nickel. It is used in a variety of industrial applications due to its strength, durability, and resistance to environmental factors. Stainless tube can be found in different forms, including seamless, welded, and brazed, and it is available in a range of sizes and specifications to meet specific needs.
Key Properties of Stainless Tubing
Understanding the properties of stainless tubing helps in appreciating its benefits:
- Corrosion Resistance: Stainless tubing is highly resistant to rust and corrosion, making it suitable for harsh environments.
- Strength and Durability: It offers high tensile strength and durability, which are crucial for withstanding high pressures and mechanical stress.
- Temperature Tolerance: Stainless tube can operate effectively across a wide range of temperatures, from cryogenic to high-heat conditions.
- Aesthetic Appeal: Its smooth, shiny surface enhances the appearance of machinery and equipment.
Benefits of Stainless Tubing in Industrial Applications
Stainless tubing provides numerous advantages that make it a preferred choice across various industries. Here are the top benefits:
Enhanced Corrosion Resistance
One of the most significant benefits of stainless tube is its exceptional resistance to corrosion. This property is especially valuable in industries where exposure to chemicals, moisture, and other corrosive elements is common.
- Chemical Processing: Stainless tube resists chemical reactions, making it ideal for handling aggressive chemicals.
- Marine Applications: It withstands saltwater and high humidity, preventing rust and degradation.
High Strength and Durability
Stainless tubing is renowned for its strength and durability, which are essential for industrial applications requiring robust materials.
- Pressure Systems: It can endure high-pressure conditions without compromising structural integrity.
- Mechanical Stress: Its strength makes it suitable for applications involving significant mechanical stress and wear.
Temperature Tolerance
The ability of stainless tubing to perform across a wide range of temperatures adds to its versatility.
- Cryogenic Temperatures: It remains stable and reliable at extremely low temperatures, making it suitable for cryogenic applications.
- High-Temperature Applications: Stainless tube can handle high temperatures without losing its structural properties, making it ideal for high-heat environments.
Low Maintenance Requirements
The durability and resistance of stainless tube lead to lower maintenance needs, reducing long-term operational costs.
- Reduced Corrosion: Less frequent replacement and maintenance are needed due to its corrosion resistance.
- Ease of Cleaning: Its smooth surface is easy to clean, making it suitable for sanitary applications.
Aesthetic and Functional Benefits
In addition to its practical benefits, stainless tube also offers aesthetic and functional advantages.
- Appearance: Its shiny, smooth surface adds a clean, professional look to equipment and installations.
- Versatility: It can be easily fabricated into various shapes and sizes, fitting a wide range of industrial applications.
Environmental and Safety Considerations
Using stainless tubing contributes to environmental sustainability and safety.
- Recyclability: Stainless steel is fully recyclable, contributing to environmentally-friendly practices.
- Safety: Its non-reactive properties make it safer for handling food, pharmaceuticals, and other sensitive materials.
Cost-Effectiveness
While stainless tubing can have a higher initial cost compared to other materials, its long-term benefits offer cost savings.
- Longevity: Its durability and low maintenance requirements lead to lower replacement and repair costs.
- Efficiency: Improved performance and reduced downtime contribute to overall cost savings in industrial operations.
Key Specifications and Types of Stainless Tubing
To better understand the options available, here’s a table outlining key specifications and types of stainless tubing:
Specification | Description |
---|---|
Material Grades | Common grades include 304, 316, and 321 stainless steel. |
Types | Seamless, welded, and brazed tubing. |
Wall Thickness | Available in various wall thicknesses, typically ranging from 0.020″ to 0.500″. |
Diameter | Standard diameters range from 1/8″ to 12″ or more. |
Finishes | Can include bright annealed, polished, or mill finishes. |
Temperature Range | Operates effectively from cryogenic temperatures up to 1,200°F (649°C). |
Pressure Ratings | Varies by tubing size and wall thickness; check specifications for exact ratings. |
Applications of Stainless Tubing
Stainless tubing is used in a variety of industrial applications. Here are some key areas where it excels:
Chemical and Pharmaceutical Industries
In these industries, stainless tube is used to handle chemicals and pharmaceuticals safely and efficiently. Its corrosion resistance and ease of cleaning make it ideal for applications requiring strict hygiene and durability.
Oil and Gas Industry
Stainless tubing is employed in the oil and gas industry for its strength and resistance to corrosive substances, making it suitable for pipelines and equipment exposed to harsh conditions.
Food and Beverage Industry
The non-reactive nature of stainless tube ensures that it does not contaminate food or beverages. It is used in processing, handling, and packaging equipment in this sector.
Aerospace and Automotive
In aerospace and automotive applications, stainless tubing’s strength, durability, and temperature tolerance make it suitable for structural components, fuel lines, and hydraulic systems.
Installation and Maintenance of Stainless Tubing
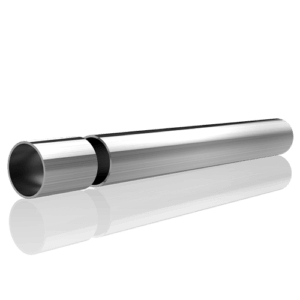
Proper installation and maintenance are key to ensuring the performance and longevity of stainless tube. Here are some best practices:
Installation Tips
- Cutting and Fitting: Use appropriate tools and techniques to cut and fit stainless tubing to avoid damage and ensure a proper seal.
- Joining Methods: Depending on the application, use welding, brazing, or mechanical fittings to join stainless tube securely.
- Cleaning: Clean tubing before installation to remove any contaminants or debris.
Maintenance Practices
- Inspection: Regularly inspect stainless tube for signs of wear, corrosion, or damage.
- Cleaning: Clean tubing as needed to maintain its appearance and performance. Avoid abrasive cleaners that can damage the surface.
- Replacement: Replace damaged or worn tubing to ensure continued safety and efficiency.
Conclusion
Stainless tubing offers numerous benefits that make it a valuable material in various industrial applications. Its corrosion resistance, strength, durability, and temperature tolerance provide reliable performance across a range of environments. By understanding the advantages of stainless tubing and following best practices for installation and maintenance, you can maximize its benefits and contribute to the success of your industrial operations. Whether in chemical processing, aerospace, or food and beverage industries, stainless tube remains a top choice for achieving high performance and efficiency.
FAQ
Q:What are the most common grades of stainless tubing?
A:The most common grades of stainless tubing are 304, 316, and 321. Each grade offers different properties suitable for various applications. Grade 304 is widely used for general purposes, while 316 is preferred for its superior corrosion resistance, and 321 is known for its high-temperature stability.
Q:Can stainless tube be used for high-temperature applications?
A:Yes, stainless tube is suitable for high-temperature applications. It can operate effectively at temperatures up to 1,200°F (649°C) depending on the grade and specifications.
Q:How should stainless tubing be cleaned?
A:Stainless tubing should be cleaned with non-abrasive cleaners and soft cloths to prevent scratching. For thorough cleaning, use mild detergents and water, and ensure that the tubing is thoroughly rinsed and dried.
Q:What is the difference between seamless and welded stainless tube?
A:Seamless stainless tube is manufactured without any welds, providing a uniform and smooth surface. Welded tubing, on the other hand, is made by welding two edges together, which can be more cost-effective but may have slight variations in strength compared to seamless tubing.
Q:How do I choose the right type of stainless tubing for my application?
A:Consider factors such as the operating environment, pressure and temperature requirements, and the type of fluid being transported. Refer to industry standards and consult with suppliers or engineers to select the appropriate grade, type, and specifications of stainless tubing for your specific application.