Welcome to My Blog!
Before we dive into the content, I’d love for you to join me on my social media platforms where I share more insights, engage with the community, and post updates. Here’s how you can connect with me:
Facebook:https://www.facebook.com/profile.php?id=100090063158454
Now, let’s get started on our journey together. I hope you find the content here insightful, engaging, and valuable.
Table of Contents
Introduction
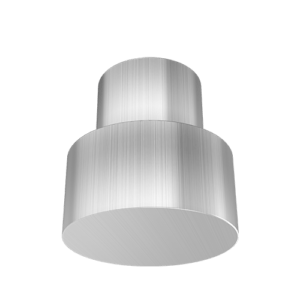
In the world of stainless steel, there are numerous grades to choose from, each designed to meet specific needs. Among the most commonly used are 410 stainless steel and 304 stainless steel. These two materials have distinct characteristics that make them suitable for different applications. If you’re considering which one to use for your next project, understanding the differences between them is crucial. This article will delve into the 7 key differences between 410 stainless steel and 304 stainless steel, providing you with the necessary insights to make an informed decision.
Composition and Structure of 410 Stainless Steel vs 304
The composition of stainless steel plays a significant role in determining its properties. Understanding the differences in the material makeup of 410 and 304 stainless steel is essential.
410 Stainless Steel Composition:
- 11.5-13.5% Chromium
- 0.15% Max Carbon
- Manganese, Silicon, and Trace Elements
304 Stainless Steel Composition:
- 18-20% Chromium
- 8-10% Nickel
- Manganese, Silicon, and Trace Elements
Key Takeaway: While both types of stainless steel contain chromium, 410 has less chromium and no nickel, while 304 contains higher chromium and nickel content, which greatly impacts their corrosion resistance.
Corrosion Resistance: 410 Stainless Steel vs 304
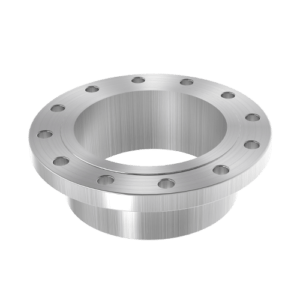
One of the key differences between 410 stainless steel and 304 stainless steel is their resistance to corrosion. This property is critical, especially in industries where stainless steel will be exposed to moisture, chemicals, or high temperatures.
- 304 Stainless Steel is known for its excellent resistance to oxidation and corrosion in a wide range of environments, including acidic and alkaline environments. It is often used in industries like food processing and medical equipment.
- 410 Stainless Steel, while still resistant to corrosion, is more prone to rusting in harsh environments due to its lower chromium and lack of nickel. It is better suited for applications that require hardness and wear resistance rather than corrosion resistance.
Key Takeaway: If your project requires superior corrosion resistance, 304 stainless steel is the better choice. However, if wear resistance is a priority, 410 stainless steel may be more appropriate.
Strength and Hardness of 410 Stainless Steel vs 304
The mechanical properties of stainless steel are vital for understanding how the material will perform under stress, heat, or mechanical wear. Here’s a comparison of the strength and hardness of both stainless steel grades:
- 304 Stainless Steel: Offers good strength but is generally more ductile and flexible than 410. This makes it ideal for forming and welding, especially in applications where complex shapes are required.
- 410 Stainless Steel: Has higher hardness due to the higher carbon content and martensitic structure. This makes it suitable for applications requiring more strength and wear resistance but makes it harder to weld and shape compared to 304.
Key Takeaway: For applications requiring superior hardness, 410 stainless steel is the best option. However, for general strength and flexibility, 304 stainless steel is more versatile.
Welding Capabilities: 410 Stainless Steel vs 304
Welding is an essential aspect of many industrial applications. However, not all types of stainless steel are equally easy to weld.
- 304 Stainless Steel: Due to its austenitic structure, 304 stainless steel is easier to weld and does not require pre- or post-welding heat treatment. It is commonly used in applications where welding is needed for structural integrity.
- 410 Stainless Steel: Welding 410 stainless steel is more challenging because of its higher carbon content. It is more susceptible to cracking during the welding process, and special care is needed to prevent it. Additionally, 410 may require heat treatment after welding to ensure strength and durability.
Key Takeaway: For projects that involve welding, 304 stainless steel is the easier option, while 410 requires more expertise and specific conditions to avoid issues.
Cost Comparison: 410 Stainless Steel vs 304
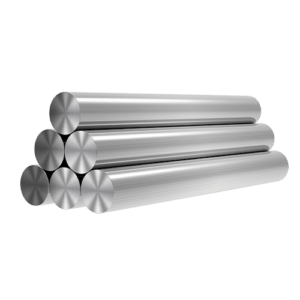
Cost is always an important factor in decision-making for any project. While both 410 and 304 stainless steels are relatively affordable, there are differences in price due to their composition and properties.
- 304 Stainless Steel: Generally more expensive due to its higher nickel content, which increases production costs. However, its corrosion resistance and ease of fabrication make it more cost-effective for certain applications in the long run.
- 410 Stainless Steel: More cost-effective upfront due to the lower cost of materials (no nickel). However, the increased wear over time in harsh environments may result in higher maintenance costs.
Key Takeaway: 410 stainless steel offers a more affordable option upfront, but 304 may provide better value over time due to its durability.
Applications of 410 Stainless Steel vs 304
Each type of stainless steel has its ideal use case based on its properties. Here are some common applications for both materials:
Stainless Steel Grade | Common Applications |
---|---|
410 Stainless Steel | Knife blades, cutting tools, medical tools, petrochemical equipment |
304 Stainless Steel | Kitchen appliances, medical instruments, food processing equipment, architectural applications |
Key Takeaway: 410 is preferred in applications requiring hardness and strength, while 304 is the go-to choice for corrosion-resistant applications.
Conclusion
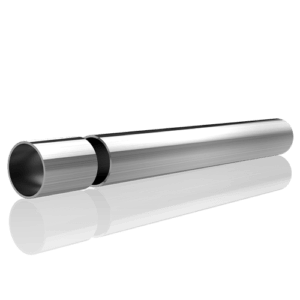
Choosing between 410 stainless steel and 304 stainless steel depends on your specific needs, including the environment, application, and desired mechanical properties. While 304 stainless steel excels in corrosion resistance, 410 stainless steel stands out for its hardness and strength. Understanding the key differences between these two materials will help you select the right one for your project.
FAQ
Which is more corrosion-resistant: 410 or 304 stainless steel?
304 stainless steel is more resistant to corrosion, making it ideal for environments exposed to moisture and chemicals.
Can I weld 410 stainless steel easily?
Welding 410 stainless steel is more difficult than 304, as it requires special attention to avoid cracking.
Which stainless steel is better for industrial applications?
Both are used in industrial applications, but 304 is preferred for its resistance to corrosion, while 410 is better suited for applications requiring higher strength and hardness.
Is 304 stainless steel more expensive than 410?
Yes, 304 stainless steel is typically more expensive due to the higher nickel content in its composition.
Which type of stainless steel should I choose for a food processing facility?
304 stainless steel is the better choice due to its excellent corrosion resistance, which is essential in the food industry.