Machinability, in the context of metalworking, is a critical factor that determines how easily a material can be shaped, cut, drilled, or otherwise manipulated during the machining process. When it comes to 316 stainless steel round bars, renowned for their corrosion resistance and durability, evaluating machinability is of paramount importance. In this in-depth guide, we will explore the intricate world of assessing the machinability of 316 stainless steel, shedding light on the factors, tests, and considerations that play a pivotal role in this evaluation.
Understanding Machinability
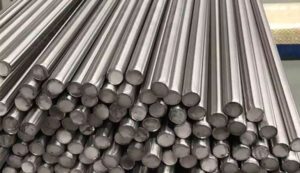
What Is Machinability?
Before we delve into the specifics of evaluating the machinability of 316 stainless steel round bars, it’s crucial to comprehend the concept of machinability itself:
Machinability refers to a material’s ability to be cut, shaped, or otherwise altered with ease during machining operations. It encompasses a range of factors, including the material’s physical and mechanical properties, as well as how it interacts with cutting tools and processes.
Factors Influencing the Machinability of 316 Stainless Steel
The machinability of 316 stainless steel round bars is influenced by a multitude of factors, each playing a unique role in determining how effectively the material can be machined. Let’s explore these factors in detail:
1. Alloy Composition
316 stainless steel contains elements like chromium, nickel, and molybdenum, which contribute to its corrosion resistance but can also affect machinability. The alloy’s composition can influence factors such as tool wear and chip formation.
2. Hardness
The hardness of 316 stainless steel is typically in the range of 25 to 39 HRC (Rockwell Hardness C scale). Higher hardness can make machining more challenging and may require specialized tooling.
3. Work Hardening
316 stainless steel exhibits work hardening, which means it becomes harder and more resistant to machining as it is worked. This can necessitate frequent tool changes to maintain machining efficiency.
4. Cutting Tools
The selection of cutting tools is crucial. Carbide or high-speed steel tools are often preferred for machining 316 stainless steel due to their durability and heat resistance.
5. Cutting Speed and Feed
Optimizing cutting speed and feed rates is essential to prevent excessive heat generation, tool wear, and work hardening. The right combination depends on factors like tool material and workpiece hardness.
6. Coolant and Lubrication
Using coolants and lubricants during machining helps dissipate heat, reduces friction, and prolongs tool life. It also aids in maintaining surface finish quality.
Evaluating Machinability through Tests
Several standardized tests and methods are used to assess the machinability of materials like 316 stainless steel. These tests provide valuable data for manufacturers and engineers:
1. Turning Test
In the turning test, a sample of 316 stainless steel is machined using specific cutting conditions and tools. Parameters such as tool wear, cutting forces, and surface finish are measured and analyzed to evaluate machinability.
2. Drilling Test
Drilling tests involve drilling holes in 316 stainless steel round bars, measuring parameters like tool life, hole quality, and drilling forces. This test is particularly relevant for applications requiring drilled holes.
3. Tapping Test
Tapping involves threading holes in the material. Tapping tests assess the ease of tapping and the quality of threads produced, providing insights into machinability.
4. Chip Formation Analysis
The study of chip formation during machining can reveal valuable information about the material’s machinability. Short, continuous chips are preferable, as they indicate efficient machining.
5. Surface Finish Measurement
Surface finish is a critical aspect of machined components. Measuring surface roughness and analyzing the quality of the finished surface is an integral part of machinability evaluation.
Factors to Consider in Machining 316 Stainless Steel
When machining 316 stainless steel round bars, several factors should be considered to optimize the process:
1. Tool Selection
Choosing the right cutting tools, such as carbide or high-speed steel, is crucial for effective machining.
2. Tool Geometry
Tool geometry, including rake angles and relief angles, should be carefully selected to suit the material and machining operation.
3. Cutting Speed and Feed Rate
Optimizing cutting speed and feed rates helps control heat generation and maintain tool life.
4. Coolant and Lubrication
Using appropriate coolants and lubricants helps in dissipating heat and reducing friction during machining.
5. Workholding
Secure workholding methods are essential to prevent vibrations and ensure stability during machining.
FAQ: Answering Common Queries
Q1. What makes 316 stainless steel challenging to machine?
The alloy’s composition, hardness, and work-hardening behavior can make 316 stainless steel challenging to machine. It requires the use of suitable tools and machining parameters.
Q2. Can 316 stainless steel be machined using common machining processes?
Yes, 316 stainless steel can be machined using common processes such as turning, drilling, and milling. However, it may require specialized tooling and careful optimization of cutting parameters.
Q3. Are there any alternatives to machining 316 stainless steel?
In cases where machining is challenging, other processes like waterjet cutting or laser cutting may be considered as alternatives for shaping 316 stainless steel.
Q4. How can machinability testing benefit manufacturers and engineers?
Machinability testing provides valuable data to optimize machining processes, select appropriate tools, and improve overall manufacturing efficiency. It helps in reducing costs and enhancing product quality.
In Conclusion
Evaluating the machinability of 316 stainless steel round bars is a multifaceted process that involves considering various factors, conducting standardized tests, and making informed choices in tooling and machining parameters. Despite its challenges, 316 stainless steel remains a sought-after material due to its exceptional corrosion resistance and durability, making it worth the effort to master the art of machining for various critical applications across industries.