Introduction
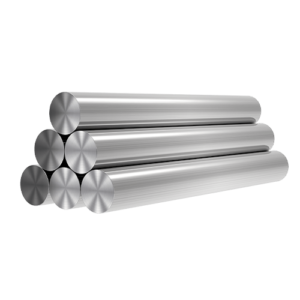
Stainless steel has become an indispensable material in various industries due to its exceptional corrosion resistance, durability, and versatility. Among the plethora of stainless steel grades available, 410 stainless steel stands out for its unique properties and wide-ranging applications. In this blog post, we delve into the applications and advantages of 410 nonrust steel rod, exploring its diverse uses across industries and highlighting its superior characteristics.
Understanding 410 Stainless Steel Bar
410 stainless steel is a versatile martensitic stainless steel alloy containing 11.5-13.5% chromium, which imparts excellent corrosion resistance and high strength properties. Additionally, it contains a small amount of carbon, providing it with exceptional hardness and wear resistance. These properties make 410 stainless steel bars ideal for a multitude of applications across various sectors.
Applications of 410 Stainless Steel Bars
410 nonrust steel rods find extensive usage across different industries due to their exceptional properties. Some key applications include:
- Automotive Industry: In the automotive sector, 410 nonrust steel rods are utilized in components such as exhaust systems, mufflers, and catalytic converters due to their high temperature and corrosion resistance.
- Construction and Architecture: The construction industry utilizes 410 nonrust steel rods for structural components, reinforcement bars, and architectural elements where corrosion resistance and durability are paramount.
- Manufacturing: In manufacturing processes, 410 nonrust steel rods are used for producing shafts, fasteners, valves, and pump parts due to their excellent machinability, hardness, and corrosion resistance.
- Oil and Gas Industry: 410 nonrust steel rods are employed in the oil and gas sector for applications such as downhole tools, pump shafts, and valve components due to their resistance to corrosive environments and high temperatures.
- Medical Equipment: In the medical field, 410 nonrust steel rods find application in surgical instruments, dental tools, and medical implants due to their biocompatibility, strength, and corrosion resistance.
Advantages of 410 Stainless Steel Bars
The advantages of using 410 stainless steel bars are numerous, making them a preferred choice in various industries:
- Corrosion Resistance: 410 nonrust steel rods exhibit excellent resistance to corrosion in both mild and harsh environments, including exposure to moisture, chemicals, and atmospheric conditions.
- High Strength: With a martensitic structure, 410 nonrust steel rods offer high tensile and yield strength, making them suitable for applications requiring robust and durable materials.
- Hardness and Wear Resistance: The addition of carbon imparts exceptional hardness to 410 nonrust steel rods, enabling them to withstand abrasion, wear, and deformation in demanding operating conditions.
- Machinability: 410 nonrust steel rods possess good machinability, allowing for ease of fabrication and machining into various shapes and sizes, thereby enhancing their versatility in manufacturing processes.
- Cost-Effectiveness: Compared to other stainless steel grades, 410 nonrust steel rods offer a cost-effective solution without compromising on performance, making them a preferred choice for numerous applications.
410 Stainless Steel Bar Composition
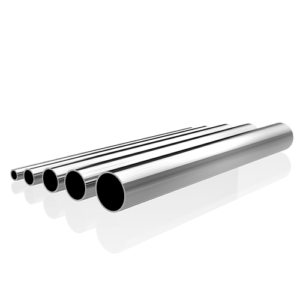
Below is a table illustrating the typical composition of 410 stainless steel bars:
Element | Composition (%) |
---|---|
Carbon (C) | 0.15 max |
Chromium (Cr) | 11.5 – 13.5 |
Manganese (Mn) | 1.0 max |
Silicon (Si) | 1.0 max |
Phosphorus (P) | 0.04 max |
Sulfur (S) | 0.03 max |
Conclusion
In conclusion, 410 stainless steel bars offer a myriad of advantages and applications across diverse industries, ranging from automotive and construction to manufacturing and medical sectors. With their exceptional corrosion resistance, high strength, and durability, 410 stainless steel bars continue to unlock new potentials in various engineering and industrial applications.
FAQ
Q:What is the difference between 410 and 416 stainless steel bars?
A:While both 410 and 416 stainless steel bars belong to the martensitic family, they differ in their sulfur content. 410 stainless steel bars have lower sulfur content, making them more suitable for welding applications, whereas 416 stainless steel bars contain higher sulfur content, imparting better machinability but reduced weldability.
Q:Can 410 stainless steel bars be heat treated?
A:Yes, 410 stainless steel bars can be heat treated to achieve desired mechanical properties. Typical heat treatment processes include annealing, quenching, and tempering, which can enhance hardness, strength, and toughness as per application requirements.
Q:What are the limitations of using 410 stainless steel bars?
A:While 410 stainless steel bars offer excellent corrosion resistance and strength, they may exhibit reduced toughness and ductility compared to austenitic stainless steel grades. Therefore, they may not be suitable for applications requiring extreme cryogenic temperatures or severe impact loading.
Q:How do you maintain 410 stainless steel bars?
A:Proper maintenance of 410 stainless steel bars involves regular cleaning to remove contaminants and prevent corrosion. Additionally, applying protective coatings or passivation treatments can enhance their corrosion resistance and prolong service life.
Are 410 stainless steel bars suitable for food-grade applications?
While 410 stainless steel bars offer good corrosion resistance, they may not be recommended for direct food contact applications due to their lower chromium content compared to austenitic stainless steel grades such as 304 or 316. However, they can be used in food processing equipment and components where direct food contact is avoided.