Introduction
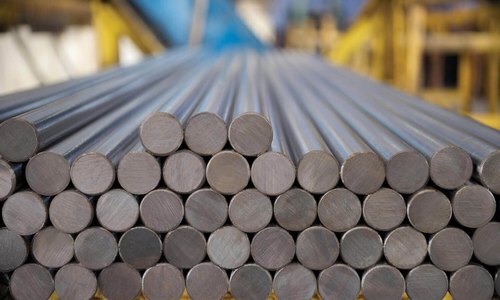
430 stainless steel is a ferritic stainless steel grade that is widely used for applications requiring moderate corrosion resistance combined with good formability and weldability. As the name suggests, 430 stainless contains approximately 16-18% chromium as its major alloying element. However, there are some key aspects regarding the composition and properties of this useful grade of stainless steel that many people may not be familiar with.
In this blog post, I aim to highlight some of the lesser known facts about 430 stainless steel composition that I wish more people understood. We’ll cover the definitions of key terms, standard specifications, effects of alloying elements, typical mechanical properties, common applications, and comparisons to other popular stainless steel grades. My goal is that after reading this, you’ll have a more thorough understanding of what sets 430 stainless apart from other alloys.
Overview of 430 Stainless Steel Composition
Alloying Element | Percent Composition |
---|---|
Carbon (C) | 0.12% max |
Silicon (Si) | 1.00% max |
Manganese (Mn) | 1.00% max |
Phosphorus (P) | 0.04% max |
Sulfur (S) | 0.03% max |
Chromium (Cr) | 16.00-18.00% |
Nickel (Ni) | 0.75% max |
Nitrogen (N) | 0.10% max |
Iron (Fe) | Balance |
As seen above, chromium is by far the most significant alloying element. The 16-18% chromium content gives 430 its stainless steel properties, allowing it to achieve moderate corrosion resistance. The low carbon content also contributes to good weldability and formability.
Now let’s analyze some of these compositional limits in more detail…
Key Points on Chromium and Carbon Content
Chromium Content
The 16-18% chromium range is intentionally kept at modest levels. Higher chromium increases corrosion resistance, but also impacts workability and cost. The balance struck by 430 stainless allows it to offer a combination of moderate corrosion resistance and good manufacturability at relatively low cost. This makes it economically preferable for many non-critical applications compared to highly-alloyed stainless grades.
Carbon Content
The 0.12% maximum carbon limit enables good forming and welding characteristics. As carbon content increases, stainless steel becomes stronger but loses ductility and becomes more difficult to weld or machine. The low carbon content gives 430 stainless improved fabricability relative to higher-carbon “martensitic” stainless alloys like 410 or 420. This comes at the expense of reduced strength.
So in summary, the restricted chromium and carbon levels optimize the balance of properties like corrosion resistance, workability, weldability, and cost. Next we’ll see how other alloying elements fit into the picture…
Effects of Other Alloying Elements
While chromium and carbon have the most influence, other alloying elements in 430 stainless fine tune certain properties:
- Silicon – Contributes to better oxidation and corrosion resistance in high temperature service environments. Up to 1% Si is allowed.
- Manganese – Primarily deoxidizes and desulfurizes steel during melting. Up to 1% Mn content is permitted for 430 stainless.
- Phosphorus & Sulfur – Impurities that can negatively impact ductility and weldability if present in excessive amounts. Tight limits of 0.04% max P and 0.03% max S are placed to prevent issues.
- Nickel – A common stainless alloying element. Only small residual amounts (0.75% max) are allowed in 430, as higher Ni would drastically increase cost without benefitting the intended applications of 430 stainless.
- Nitrogen – Like nickel, most grades allow higher N content but it is restricted in 430 stainless (0.10% max) due to economic considerations.
In short, these other alloying elements have small effects in 430 stainless steel or are minimized due to cost considerations relative to the intended end uses.
Overview of Mechanical Properties
Here is an overview of the minimum mechanical properties specified for 430 stainless steel in annealed condition per ASTM A240 standard:
Mechanical Property | Minimum Specification |
---|---|
Tensile Strength | 51 ksi (350 MPa) |
Yield Strength | 28 ksi (205 MPa) |
Elongation | 20% |
A few key things to note:
- Tensile and yield strengths are moderately low compared to highly-alloyed stainless steels due to the lower alloy content and higher ferrytic iron phase.
- Elongation is quite good owing to the low carbon concentration – over 20% elongation demonstrates excellent ductility.
- Mechanical strength can be substantially increased through processes like cold working. Yield strength over 90 ksi (620 MPa) is possible.
So while 430 stainless steel exhibits only moderate strength (which helps formability), the excellent ductility enables good fabricability for shaped components and deep drawing applications.
Unique Applications and Uses
Thanks to its favorable balance of corrosion resistance, ease of fabrication, and low cost, 430 stainless steel is used across a wide variety of application areas including:
- Appliances: Washer drums, dishwasher components, refrigeration parts
- Architecture: Roofing, wall panels, trim accents
- Automotive: Mufflers, cladding, trim parts
- General Manufacturing: Machine guards, fasteners, shafts, valves, mining screens
Owing to good formability and weldability, 430 stainless can be fabricated into complex shapes – an advantage over higher alloy alternatives like 304 stainless steel. Parts like spinning manifolds and catalytic converter housings take advantage of these fabrication abilities.
Comparison to Other Stainless Grades
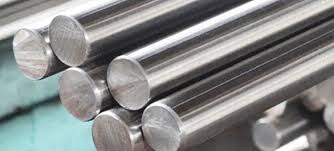
It’s also helpful to understand how 430 stainless steel differs from other popular stainless steel grades:
Alloy Type | Key Properties | Typical Applications |
---|---|---|
430 Stainless | Lower corrosion resistance but better formability and weldability versus 304. More economical. | Appliances, automotive exhaust components, architectural accents. |
304 Stainless | Higher corrosion resistance than 430 thanks to 18-20% chromium and 8-10.5% nickel additions. More difficult to weld and fabricate. | Chemical equipment, kitchenware, tanks, marine components, construction materials. |
410 Stainless | Similar corrosion resistance to 430 but higher strength from increased carbon content. Less formable. | Mechanical parts including fasteners, pumps, and valves. |
There are certainly scenarios where the higher alloy grades outperform 430 stainless. But for applications not requiring exceptional corrosion resistance, 430 provides the best economic solution that maximizes fabricability.
Conclusion
In closing, while 430 stainless steel plays a critical role across many industries, its composition and performance capabilities are not as widely understood compared to higher-end alloys like 304. My goal was to draw attention to several underappreciated aspects of 430 stainless steel:
- The 16-18% chromium and restricted 0.12% max carbon content strike an optimal balance of moderate corrosion resistance, excellent formability and weldability, and economic affordability
- Mechanical properties are enhanced by the low carbon level, providing over 20% elongation and ability for significant cold working
- Applications take advantage of good fabricability, weldability, and moderate corrosion resistance at lower alloy cost versus 304 or 316 stainless
I hope this provided useful insights into this versatile stainless grade. Please leave any questions below!
FAQ
Q: What is the difference between ferritic and austenitic stainless steel grades?
A: Ferritic stainless steels like 430 have a ferrite iron crystalline structure allowing good ductility for fabrication. Austenitic stainless steels like 304 contain nickel to attain an austenitic structure. This increases strength and corrosion resistance but decreases fabricability.
Q: Can you weld 430 stainless steel?
A: Yes, the low carbon composition enables excellent weldability. Common welding methods used for 430 stainless include MIG, TIG, laser, and spot welding. Proper heat input levels and shielding should be followed to avoid chromium carbide precipitates along grain boundaries.
Q: What is annealed 430 stainless steel?
A: Annealing refers to heat treating at 1850-2100°F (1010-1150°C) then slowly cooling to achieve softened, ductile condition. Annealed structure provides lowest hardness and highest corrosion resistance. ASTM A240 specifications give minimum mechanical properties for annealed condition.