Introduction
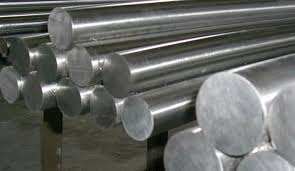
When it comes to selecting the right stainless steel for your project, the choice between 410 and 304 can be pivotal. Both offer unique properties and advantages, catering to different needs and applications. In this comprehensive guide, we’ll delve into the characteristics, applications, and comparative analysis of 410 stainless steel and 304 stainless steel, aiding you in making an informed decision for your project requirements.
Characteristics of 410 Stainless Steel
410 stainless steel stands as a formidable member of the martensitic stainless steel family, renowned for its exceptional blend of corrosion resistance, strength, and hardness. Constituting a crucial alloying element, chromium content within the range of 11.5%-13.5% forms the backbone of its corrosion-resistant properties. This unique composition renders 410 stainless steel highly resistant to various corrosive environments, including those exposed to moisture, atmospheric conditions, and mild chemical agents.
Moreover, what sets 410 stainless steel apart is its innate ability to undergo heat treatment processes, thereby unlocking its full potential in terms of mechanical properties. Through careful manipulation of temperature and cooling rates, the steel’s microstructure can be tailored to achieve desired levels of strength, hardness, and toughness. This versatility in heat treatment empowers 410 stainless steel to excel across a diverse spectrum of applications, ranging from industrial machinery components to precision tools and surgical instruments.
The combination of robust corrosion resistance, formidable strength, and customizable mechanical properties makes 410 stainless steel an indispensable material in numerous industries. Whether it’s withstanding harsh environmental conditions, enduring high-stress applications, or maintaining dimensional stability in precision engineering, 410 stainless steel continues to prove its mettle as a reliable and versatile alloy.
Characteristics of 304 Stainless Steel
304 stainless steel, a distinguished member of the austenitic stainless steel family, stands as a testament to versatility and unparalleled corrosion resistance. Characterized by its austenitic crystalline structure, 304 stainless steel boasts a composition comprising 18%-20% chromium and 8%-10.5% nickel, which forms the cornerstone of its exceptional corrosion-resistant properties. This alloy’s chromium content ensures robust resistance against a myriad of corrosive agents, including acids, alkaline solutions, and chloride ions, rendering it particularly adept at withstanding challenging environmental conditions.
However, it is the addition of nickel that truly elevates the corrosion resistance of 304 stainless steel, especially in acidic environments. Nickel serves as a potent alloying element, augmenting the steel’s ability to resist corrosion by enhancing its passivation and forming a protective oxide layer on its surface. Consequently, 304 stainless steel emerges as a stalwart contender in applications exposed to aggressive chemical environments, such as chemical processing plants, pharmaceutical facilities, and marine installations.
Beyond its exceptional corrosion resistance, 304 stainless steel is revered for its exceptional ease of fabrication and formability. Its innate ductility and malleability allow for effortless shaping, bending, and welding, facilitating seamless integration into various manufacturing processes. Whether it’s intricate machining operations, intricate welding assemblies, or intricate forming techniques, 304 stainless steel emerges as a preferred choice, offering unparalleled versatility and adaptability across diverse industrial sectors.
Comparative Analysis
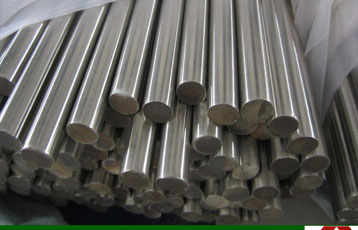
Corrosion Resistance
One of the primary factors to consider when choosing between 410 and 304 stainless steel is corrosion resistance. While both offer corrosion resistance properties, 304 stainless steel outperforms 410 stainless steel in corrosive environments, particularly in acidic conditions. Therefore, if your project involves exposure to corrosive substances, 304 stainless steel may be the better choice.
Tensile Strength and Hardness
410 stainless steel boasts higher tensile strength and hardness compared to 304 stainless steel. This makes it suitable for applications requiring enhanced strength and durability, such as automotive parts, industrial equipment, and tooling. However, it’s essential to consider the trade-off between strength and corrosion resistance when making your decision.
Fabrication and Weldability
304 stainless steel is known for its excellent formability and weldability, allowing for easy fabrication and assembly. In contrast, 410 stainless steel exhibits poorer weldability and may require preheating and post-weld heat treatment to avoid cracking and distortion. Therefore, the choice between the two steels depends on the specific fabrication requirements of your project.
Applications
The choice between 410 and 304 stainless steel depends on the specific requirements of your project and the environmental conditions it will be exposed to. Below is a comparison of typical applications for both steels:
Applications | 410 Stainless Steel | 304 Stainless Steel |
---|---|---|
Automotive Parts | Engine components, exhaust systems | Exhaust manifolds, trim, grills |
Industrial Equipment | Shafts, fasteners, pump parts | Pressure vessels, storage tanks, piping |
Tooling | Tool dies, cutting tools | Molds, dies, precision instruments |
Kitchen Equipment | Cutlery, kitchen utensils | Sinks, cookware, food processing equipment |
Architectural Elements | Door hardware, decorative trim | Handrails, architectural panels, facade cladding |
Conclusion
In conclusion, the choice between 410 and 304 stainless steel depends on a multitude of factors, including corrosion resistance, strength, fabrication requirements, and specific applications. While 410 stainless steel offers superior strength and hardness, 304 stainless steel excels in corrosion resistance and fabricability. Therefore, it’s essential to evaluate your project’s needs carefully and weigh the pros and cons of each steel before making a decision.
FAQ
Q: Can 410 stainless steel be used in food-grade applications?
A: While 410 stainless steel offers excellent strength and hardness, it is not typically recommended for food-grade applications due to its lower corrosion resistance compared to 304 stainless steel.
Q: Is 304 stainless steel magnetic?
A: Yes, 304 stainless steel is generally magnetic due to its austenitic crystalline structure. However, the degree of magnetism may vary depending on factors such as processing and composition.
Q: Can 410 stainless steel be welded?
A: Yes, 410 stainless steel can be welded, but it exhibits poorer weldability compared to 304 stainless steel. Preheating and post-weld heat treatment are often necessary to minimize the risk of cracking and distortion.